Huaxiao Metal – A Top Titanium Alloy Manufacturer in China
Huaxiao Metal is a leading high-performance titanium alloys supplier in China, offering a wide range of titanium-based materials, including titanium alloy for rocket fins, titanium alloy 6Al-4V, titanium tungsten alloy, nickel titanium alloy, and other premium titanium alloys. Our products are recognized for their exceptional strength, low density, excellent corrosion resistance, and outstanding performance in high-temperature and aggressive environments. These alloys are widely used across industries such as aerospace, marine, medical, automotive, and chemical processing.
As trusted experts in titanium alloys, we specialize in providing customized solutions tailored to meet the specific needs of our clients. Whether you’re looking for titanium alloy sheets, titanium alloy plates, titanium alloy bars, or specialized titanium alloys for aerospace applications, Huaxiao Metal ensures high-quality products designed for durability, reliability, and superior performance.
Our portfolio includes various titanium alloy grades, such as titanium 6Al-4V, nickel titanium alloys, and gold titanium alloys, all known for their superior properties like high tensile strength, corrosion resistance, and low thermal conductivity. These alloys offer great advantages in applications that require lightweight, high-strength materials, such as aerospace, automotive engineering, and medical implants.
We offer a broad selection of titanium alloys to suit different industries, from titanium alloy for medical implants to titanium alloy for rocket fins. Whether you need titanium gold alloy, titanium aluminum alloy, titanium tungsten alloy, or titanium-copper alloys, we provide tailored solutions to meet your requirements.
Our titanium alloys are engineered for exceptional performance in extreme conditions, offering excellent resistance to corrosion, high temperatures, and stress. For example, titanium alloy 6Al-4V (Ti-6Al-4V) is widely used in high-stress aerospace applications, while nickel titanium alloys (NiTi) are known for their remarkable shape memory and superelasticity, making them ideal for medical devices and orthodontic applications.
At Huaxiao Metal, we understand that cost-effectiveness is crucial. That’s why we offer competitive titanium alloy prices for large-scale projects, without compromising on quality. Whether you’re looking for titanium alloy for aircraft, titanium alloy for shipbuilding, or titanium alloy in dental applications, we are here to help you find the best material at the best price.
Our titanium alloys include various grades and compositions designed for specific uses, such as titanium and tungsten alloys, titanium and aluminum alloys, and titanium and nickel alloys. We provide high-performance materials for critical applications across aerospace, medical, automotive, and marine industries.
As a trusted titanium alloy supplier, we are committed to providing the highest quality materials to meet the diverse needs of our clients. Contact us today to learn more about our products, including titanium alloy for aerospace, titanium alloy for medical implants, and titanium alloy composition. We are here to help you find the perfect titanium alloy for your project.
Titanium Alloy Products
Titanium Alloy Alpha-Beta (α -β)
Titanium Alloy Alpha-Beta (α -β) Titanium Alloy Alpha-Beta (α-β): A Versatile Titanium Alloy for High-Performance Applications Titanium Alpha-Beta (α-β) alloys are a class of titanium
Titanium Alloy Beta (β)
Titanium Alloy Beta (β) Titanium Alloy Beta (β): High-Strength, Heat-Treatable Titanium for Demanding Applications Titanium Beta (β) alloys are a group of titanium alloys characterized
Titanium Alloy Alpha (α)
Titanium Alloy Alpha (α) Titanium Alloy Alpha (α): High-Strength, Corrosion-Resistant Titanium for Specialized Applications Titanium Alpha (α) alloys are a group of titanium alloys primarily
Titanium Alloy Classification
Classification of Titanium Alloys:
Titanium alloys are widely used in various high-performance applications due to their strength, light weight, and exceptional resistance to corrosion. These alloys come in different grades and compositions, each designed for specific industrial applications. As a leading supplier of titanium alloys, we offer a comprehensive range of products, including titanium alloy for rocket fins, titanium alloy 6Al-4V, nickel titanium alloy, titanium gold alloy, titanium tungsten alloy, and more. Below are some of the most common types of titanium alloys we supply:
Titanium Alloy 6Al-4V (Ti-6Al-4V):
Titanium alloy 6Al-4V is one of the most widely used titanium alloys, known for its excellent combination of strength, corrosion resistance, and light weight. It is commonly used in aerospace, medical implants, and automotive applications. As a top supplier of Ti-6Al-4V, we provide it in various forms, including sheets, bars, plates, and custom shapes.
Titanium Alloy for Rocket Fins:
Titanium alloys are often used in aerospace applications, including rocket fins, due to their high strength-to-weight ratio, resistance to high temperatures, and corrosion resistance. Titanium alloy 6Al-4V, in particular, is ideal for such demanding environments, where performance and reliability are critical.
Titanium Alloy Composition:
Titanium alloys typically consist of titanium mixed with various elements like aluminum, vanadium, nickel, and tungsten to enhance their properties. For example, titanium aluminum alloy offers excellent resistance to high temperatures, while titanium and tungsten alloys combine the lightness of titanium with the strength of tungsten for heavy-duty applications.
Gold Titanium Alloy:
Gold titanium alloys are a unique material offering the beauty and aesthetic properties of gold with the durability of titanium. These alloys are commonly used in jewelry, watches, and luxury accessories. Gold titanium alloy price can vary depending on the grade and processing, but it is highly valued for its durability and visual appeal.
Nickel Titanium Alloy (NiTi):
Nickel titanium alloys, also known as Nitinol, are famous for their unique shape memory and superelastic properties. These alloys are widely used in medical devices, orthodontics, and actuators. Nickel titanium alloy properties include high flexibility and the ability to return to their original shape when heated, making them ideal for applications requiring precision.
Titanium Tungsten Alloy:
Titanium tungsten alloys offer a combination of titanium’s lightweight properties and tungsten’s strength and density. These alloys are often used in applications like medical implants, aerospace, and heavy-duty industrial components. Titanium tungsten alloy is particularly useful in environments requiring high strength and resistance to wear.
Titanium Alloy for Medical Implants:
Titanium alloys, especially Ti-6Al-4V, are commonly used in medical implants due to their biocompatibility, strength, and resistance to corrosion. These alloys are used in joint replacements, dental implants, and surgical devices. Titanium alloy in dentistry is a popular choice for dental implants due to its ability to integrate with bone tissue effectively.
Titanium Alloy Bar:
Titanium alloy bars are available in various grades and are used in applications requiring high strength and resistance to corrosion, such as aerospace, marine, and automotive industries. Titanium alloy bar is also ideal for manufacturing parts like fasteners, shafts, and valves.
Titanium Alloy Sheets:
Titanium alloy sheets are widely used in the aerospace and automotive industries, as well as in medical applications. They are durable, lightweight, and resistant to corrosion, making them ideal for structural components in harsh environments. Titanium alloy sheets are available in different thicknesses and are supplied in standard or custom sizes to meet specific needs.
Titanium Alloy Price:
Titanium alloys are priced based on their composition, grade, and processing. For example, titanium alloy 6Al-4V is one of the most popular and cost-effective options, while gold titanium alloys and specialized alloys like titanium tungsten alloy may carry a higher price tag due to their unique properties and applications. We offer competitive titanium alloy prices to ensure our customers get high-performance materials at affordable rates.
Titanium Alloy in Aerospace:
Titanium alloys are crucial in the aerospace industry due to their high strength, lightweight nature, and resistance to high temperatures. Aerospace titanium alloys like Ti-6Al-4V and titanium-aluminum alloys are commonly used in aircraft components, including turbine engines, airframes, and fasteners.
Titanium Alloy Composition for Aerospace:
The percentage of titanium in an alloy used in aerospace typically ranges from 90% to 98%, with elements like aluminum, vanadium, and molybdenum added to enhance strength, corrosion resistance, and high-temperature performance. Titanium alloy for aerospace applications is designed to meet stringent safety and performance standards.
Titanium Alloys for High-Temperature Applications:
Certain titanium alloys, such as titanium aluminide alloy, are designed to withstand extreme temperatures. These alloys are used in turbine blades, exhaust systems, and other high-temperature applications in industries like aerospace and power generation.
Titanium Alloy vs Stainless Steel:
While both titanium alloys and stainless steel offer excellent corrosion resistance, titanium alloys are typically lighter and stronger than stainless steel, making them ideal for aerospace, automotive, and marine applications. Titanium alloy vs stainless steel often comes down to strength-to-weight ratio and specific application requirements.
Titanium Alloy Strength:
Titanium alloys are known for their strength, especially Ti-6Al-4V, which is one of the strongest and most versatile titanium alloys. Titanium alloy strength makes them ideal for applications in extreme conditions, including aerospace and military applications.
Titanium Alloy in Marine Applications:
Due to their excellent corrosion resistance, titanium alloys are widely used in marine environments. They are commonly used in shipbuilding, underwater equipment, and offshore platforms, where their ability to resist corrosion from seawater is a crucial factor.
Titanium Alloy Melting Point:
Titanium alloys generally have high melting points, with Ti-6Al-4V melting at around 1,670°C (3,038°F). This property makes them suitable for applications in extreme heat, such as jet engines, power plants, and other high-temperature environments.
Titanium Alloys in Automotive:
Titanium alloys are increasingly used in automotive applications for their lightweight properties and strength. Components such as exhaust systems, wheels, and suspension parts benefit from the performance and durability of titanium alloys.
Titanium Alloy for Jewelry:
The use of titanium alloy jewelry is becoming more popular due to its lightweight, durability, and hypoallergenic properties. Titanium alloy rings, bracelets, and other accessories are not only attractive but also offer exceptional resistance to wear and corrosion.
As a trusted supplier of titanium alloys, we offer a wide range of products, including titanium alloy plates, titanium alloy bars, and custom titanium alloys tailored to meet the needs of industries such as aerospace, automotive, medical, and marine. Whether you’re looking for titanium alloy for aerospace, titanium alloy for medical implants, or titanium alloy for high-performance applications, we are committed to delivering high-quality materials that meet your specifications and requirements. Contact us today to learn more about our products and get competitive pricing on titanium alloys.
1.Titanium Alpha (α-Titanium)
Composition:
- Titanium (99% min)
- Aluminum (2-6%)
Properties:
Titanium Alpha is known for excellent corrosion resistance, good formability, and weldability. It has low density and high strength-to-weight ratio, making it suitable for aerospace and marine applications.
Applications:
Used in aerospace components, chemical processing, marine hardware, and biomedical implants due to its strength, light weight, and resistance to harsh environments.
2.Titanium Alpha-Beta (α-β Titanium)
Composition:
- Titanium (90-99%)
- Aluminum (4-6%)
- Vanadium (3-5%)
- Iron (up to 0.5%)
Properties:
Titanium Alpha-Beta alloys combine the benefits of both α-phase (low temperature) and β-phase (high temperature) microstructures. They offer improved strength, excellent corrosion resistance, and good weldability, making them versatile for high-performance applications.
Applications:
Commonly used in aerospace, military, and chemical industries for components like aircraft structures, engine parts, and heat exchangers due to their strength, toughness, and ability to withstand high temperatures.
3.Beta (β) Titanium Alloy
Composition:
- Titanium (90-98%)
- Vanadium (10-15%)
- Iron (0.5-2%)
- Aluminum (up to 6%)
Properties:
Beta titanium alloys have a predominantly β-phase microstructure, which provides excellent strength, high hardness, and improved formability compared to α and α-β alloys. They also offer good corrosion resistance and are highly suitable for applications requiring high strength-to-weight ratios.
Applications:
These alloys are often used in aerospace components, medical implants (such as bone screws and dental implants), sporting equipment, and in the production of high-performance springs and fasteners. They are ideal for situations where strength, fatigue resistance, and lightweight are critical.
Titanium Alloy Advantages
Exceptional Corrosion Resistance: Titanium Alloys
Titanium alloys, such as Ti-6Al-4V and nickel-titanium alloys, are renowned for their outstanding corrosion resistance, making them ideal for marine, aerospace, chemical processing, and medical applications. These alloys, including titanium gold alloy and titanium aluminum alloy, are engineered to withstand harsh environments, including seawater, acidic, and high-temperature conditions. As trusted titanium alloy suppliers, we provide a wide range of high-performance alloys to meet the specific needs of industries requiring exceptional durability and long-lasting performance in corrosive and extreme environments.
High Strength and Toughness: Titanium Alloy for Demanding Applications
Titanium alloys, particularly Ti-6Al-4V titanium alloy and titanium nickel alloy, offer superior mechanical properties, including high strength, toughness, and resistance to stress corrosion cracking. These alloys are widely used in critical applications such as aerospace components, rocket fins, and marine hardware. With their exceptional fatigue resistance and high strength-to-weight ratio, titanium alloys are the perfect choice for industries that demand reliable materials for high-stress environments. As titanium alloy suppliers, we provide top-tier alloys, including the strongest titanium alloy options, ensuring superior performance in demanding conditions.
Superior Performance at High Temperatures: Titanium Alloy for Heat Resistance
Titanium alloys such as Ti-6Al-4V and titanium aluminum alloy perform exceptionally well even at elevated temperatures. These alloys are ideal for applications in aerospace, chemical reactors, and heat exchangers, offering outstanding oxidation resistance and strength retention at high temperatures. Titanium alloy for rocket fins, aerospace titanium alloys, and titanium and tungsten alloy solutions maintain their durability under extreme heat. As leading titanium alloy suppliers, we provide alloys that deliver superior performance, ensuring reliability in high-temperature applications across industries.
Versatile Applications Across Industries: Titanium Alloys for Custom Projects
Titanium alloys are known for their versatility, offering tailored solutions for industries ranging from aerospace and automotive to medical and marine. Whether you need titanium alloy for aerospace applications, titanium gold alloy for advanced engineering, or titanium copper alloy for specific industrial needs, we offer alloys that provide exceptional performance in a variety of settings. As a trusted titanium alloy supplier, we offer a diverse range of alloys, including nickel titanium alloy, tungsten titanium alloy, and aluminum titanium alloy, to meet your unique project requirements.
Excellent Fabricability and Weldability: Titanium Alloy for Precision Engineering
Titanium alloys, including Ti-6Al-4V titanium alloy and titanium gold alloy, are highly regarded for their excellent weldability and ease of fabrication. These alloys are ideal for creating custom components and precision parts, offering great versatility in complex applications. From titanium alloy sheet to titanium alloy bar, we provide materials that are easy to work with, making them perfect for industries requiring precision engineering. As leading titanium alloy suppliers, we ensure that our products can be easily fabricated to meet the specific needs of your project, whether it’s additive manufacturing of titanium alloys or traditional fabrication techniques.
High Resistance to Stress and Corrosion Cracking: Titanium Alloys for Harsh Environments
Titanium alloys, such as Ti-6Al-4V and nickel-titanium alloy, offer exceptional resistance to stress corrosion cracking, making them ideal for high-stress and highly corrosive environments. With outstanding fatigue resistance, these alloys are commonly used in aerospace, marine, and chemical processing industries. As titanium alloy suppliers, we offer alloys that are specifically designed to meet the requirements of demanding environments, including applications requiring titanium alloy for medical devices, aerospace components, and marine hardware.
Titanium Alloy Price and Availability: Competitive Pricing for Top-Quality Alloys
At our company, we strive to offer competitive pricing on a wide range of titanium alloys, including Ti-6Al-4V titanium alloy, titanium alloy bar, titanium alloy plate, and titanium alloy sheet. Whether you’re looking for titanium alloys for aerospace, medical, or industrial applications, we provide cost-effective solutions without compromising on quality. Our pricing for titanium alloy is designed to offer the best value for businesses requiring high-performance materials. As a trusted titanium alloy supplier, we ensure that our products are available at competitive rates, helping you meet your budget and performance goals.
Reliable Stock Availability and Timely Delivery: Titanium Alloy Suppliers You Can Trust
As leading titanium alloy suppliers, we maintain a reliable stock of titanium alloys, including titanium alloy plate, titanium alloy bar, and titanium alloy for aerospace applications, ensuring quick and efficient delivery to meet your business needs. Whether you need titanium alloy wheels, titanium alloy for medical applications, or specialized alloys such as titanium nickel alloy, we have the materials you need, ready to ship. Our efficient delivery system ensures that you receive your order on time, minimizing project delays.
Titanium Alloy Composition and Performance Characteristics
Titanium alloys come in various compositions, each designed to meet the specific needs of different industries. Alloys such as Ti-6Al-4V, titanium aluminum alloy, and nickel titanium alloy are known for their excellent mechanical properties, corrosion resistance, and performance under high temperatures. The precise titanium alloy composition plays a key role in determining the material’s properties, including its strength, weldability, and resistance to stress. As titanium alloy suppliers, we provide a wide range of titanium alloys with varying compositions to suit your exact application needs, whether for aerospace, marine, medical, or industrial uses.
Titanium Alloy vs Stainless Steel: Choosing the Best Material for Your Project
While stainless steel is a popular choice for many industrial applications, titanium alloys, such as Ti-6Al-4V and titanium alloy steel, offer superior strength-to-weight ratios, corrosion resistance, and performance under extreme conditions. Titanium alloys are preferred in high-performance applications such as aerospace, marine, and medical devices, where strength, weight, and durability are paramount. As titanium alloy suppliers, we offer both titanium alloy vs stainless steel comparisons and tailored recommendations to help you select the right material for your needs.
Titanium Alloy Price and Supplier Information
For the best titanium alloy price, turn to us as your trusted supplier of high-quality titanium alloys. Whether you’re searching for titanium alloy 6Al-4V, titanium alloy rims, or titanium alloy for aerospace applications, we offer competitive pricing and reliable delivery. We work closely with our clients to provide cost-effective, high-performance materials for their specific applications, from titanium alloy for 3D printing to traditional manufacturing needs. Contact us today for a quote or more information on titanium alloy suppliers and pricing.
Conclusion
As trusted titanium alloy suppliers, we offer a wide range of high-quality titanium alloys, including Ti-6Al-4V, nickel titanium alloy, titanium gold alloy, and many more. Our alloys are known for their exceptional strength, corrosion resistance, and performance in extreme environments, making them ideal for industries like aerospace, medical, automotive, and marine. With competitive pricing, reliable stock availability, and timely delivery, we are your go-to supplier for all your titanium alloy needs. Reach out to us today to learn more about our products and find the best pricing for your business.
Applications of Titanium Alloy
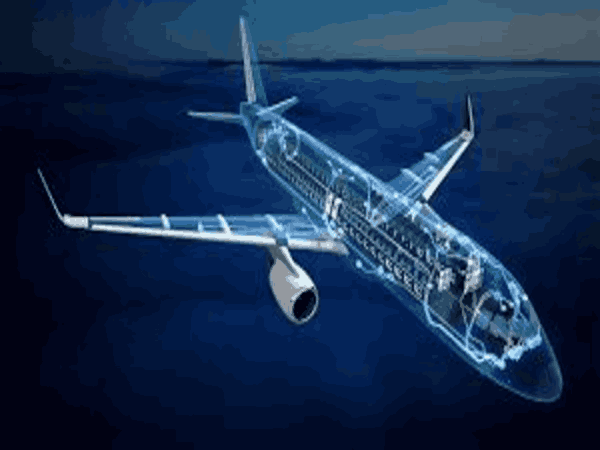
Aerospace Industry
Titanium alloys are perfect for aerospace applications, such as aircraft components and rocket parts, offering strong strength-to-weight ratio, corrosion resistance, and reliability in extreme conditions.
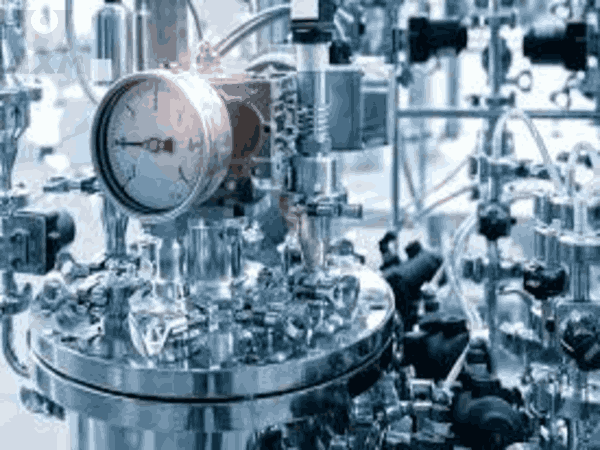
Medical Industry
Titanium alloys are ideal for the medical industry, used in implants, prosthetics, and surgical instruments, thanks to their biocompatibility, strength, and corrosion resistance. These alloys ensure durability and safe integration with the human body.

Marine Industry
Titanium alloys are ideal for the marine industry, used in shipbuilding, submarine components, and marine hardware, offering excellent corrosion resistance and strength in harsh seawater environments.
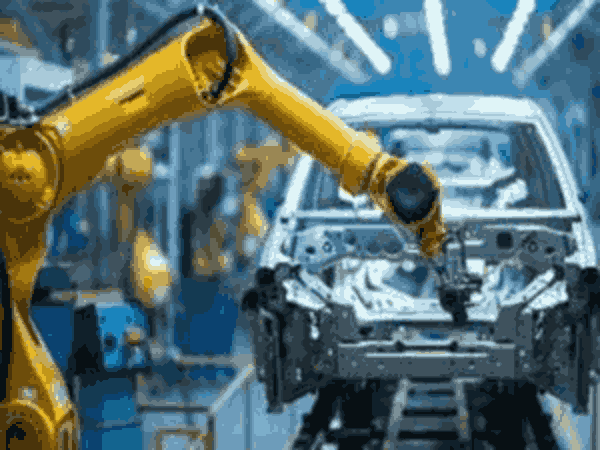
Automotive Industry
Titanium alloys are ideal for the automotive industry, used in engine components, exhaust systems, and chassis parts, providing high strength, lightweight, and corrosion resistance for enhanced performance and durability.

Sports Equipment
Titanium alloys are ideal for sports equipment, used in bicycle frames, golf clubs, and racquets, offering lightweight, strength, and durability for high-performance applications.
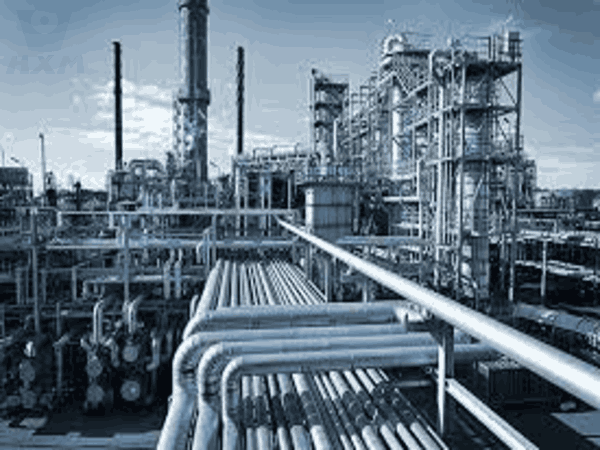
Chemical Processing Industry
Titanium alloys are ideal for the chemical processing industry, used in heat exchangers, pumps, and reactors, offering exceptional corrosion resistance and durability in aggressive chemical environments.
If you are unsure about the applications of Titanium alloys in various industries, you can contact us, Titanium alloy supplier, to learn more.
FAQ
1.Titanium vs titanium alloy?
Titanium is a pure metal, while titanium alloy is a mixture of titanium and other elements like aluminum, vanadium, or nickel, designed to enhance properties such as strength, corrosion resistance, and heat resistance. Titanium alloys offer superior performance in demanding applications compared to pure titanium, which is more suited for less harsh environments.
2.What is the melting point of titanium alloy?
The melting point of titanium alloys typically ranges between 1,600°C (2,912°F) and 1,700°C (3,092°F), depending on the specific alloy composition. For example, Ti-6Al-4V (the most commonly used titanium alloy) has a melting point around 1,660°C (3,020°F).
3.What is titanium alloy made of?
Titanium alloys are primarily composed of titanium mixed with various alloying elements to enhance specific properties. Common alloying elements include:
- Aluminum: Increases strength and reduces weight (e.g., in Ti-6Al-4V).
- Vanadium: Improves strength and fatigue resistance.
- Molybdenum: Enhances high-temperature stability and strength.
- Nickel: Improves corrosion resistance, especially in acidic environments.
- Iron: Increases strength while maintaining good formability.
- Chromium: Provides better oxidation and corrosion resistance.
These elements are combined in various proportions to create alloys suited for specific applications, such as aerospace, medical, or industrial uses.
4. How dense is titanium ?
Titanium has a density of approximately 4.43 g/cm³ (grams per cubic centimeter), making it about 60% denser than aluminum but 45% lighter than steel. This relatively low density combined with its strength and corrosion resistance makes titanium highly desirable for industries like aerospace, automotive, and medical implants.
5. How much is 1 kg of titanium?
The price of 1 kg of titanium can vary depending on factors like alloy type, market conditions, and supplier. As of recent years, the price of commercially pure titanium (CP titanium) typically ranges between $8 to $12 USD per kg, while titanium alloys like Ti-6Al-4V (the most commonly used alloy) may cost between $15 to $30 USD per kg or more, depending on the quality and specific requirements.
For exact pricing, it’s best to contact titanium suppliers or distributors for up-to-date quotes.
6. How strong is nickel titanium alloy?
Nickel-titanium alloy (Nitinol) has a tensile strength ranging from 500 to 1,400 MPa, offering both high strength and remarkable superelasticity, which allows it to return to its original shape after deformation.