Inconel 600 Alloy
Shapes:
Grades:
ASME: SB127 / N04400
JIS: G4304 / NW 4400
AISI: 400
EN: 10088-2 / 1.4360
Incoloy Alloy 825 Shapes
Monel 400 Plate & Sheet
Dimensions:
Width: 30 mm – 500 mm, 800 mm, 1000 mm, 1200 mm, 1500 mm, 1800 mm, 2200 mm, 2500 mm, 3000 mm, and other custom widths available
Length: 1500 mm, 2000 mm, 2500 mm, 3500 mm, 5000 mm, 6000 mm, 10000 mm, and other custom lengths available
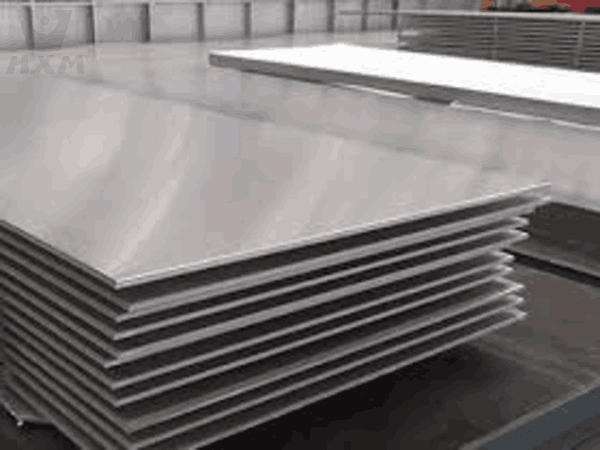
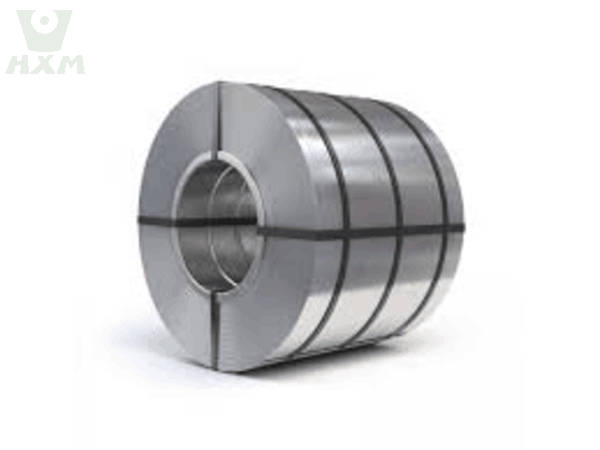
Monel 400 Coil
Dimensions:
Width: 100 mm – 1500 mm, and we also offer custom widths to meet specific project requirements.
Length: Starting from 500 mm, and custom lengths are negotiable to fit the exact needs of your installation.
Monel 400 Strip
Dimensions:
- Thickness: Typically ranging from 0.01 mm to 10 mm. This thin profile makes them suitable for applications where space is at a premium or when fine-tuned precision is required.
- Width: Available in widths from 5 mm to 500 mm, with the option for custom widths. This flexibility allows for seamless integration into diverse projects with unique size requirements.
- Length: Strips can be supplied in lengths of 1000 mm and upwards, and we also accommodate custom length requests to match your specific installation needs.
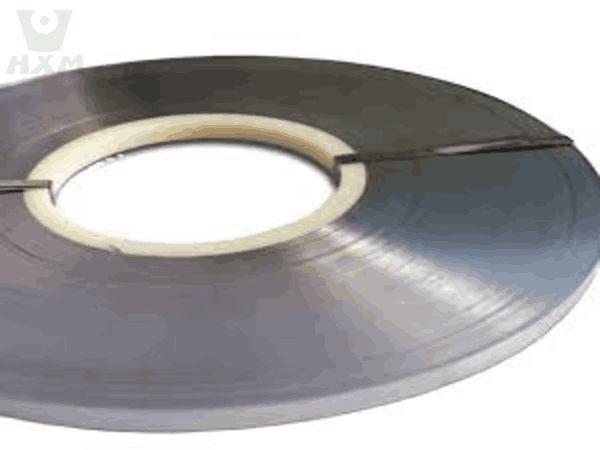
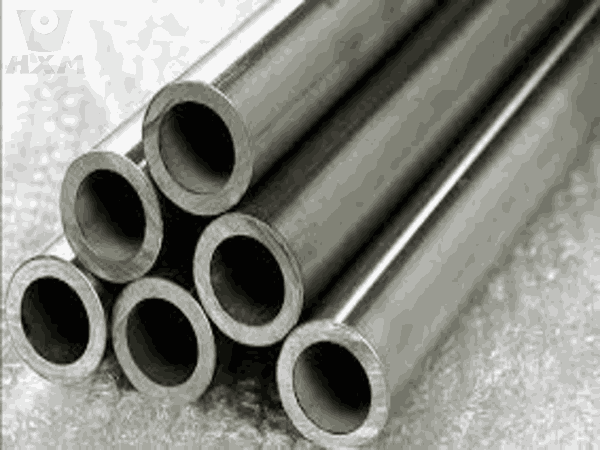
Monel 400 Pipe & Tube
Dimensions:
- Outer Diameter: Ranging from 6 mm to 508 mm, covering a wide spectrum of sizes to fit different flow requirements, whether for small-scale laboratory setups or large-scale industrial operations.
- Thickness: Varies from 0.5 mm to 50 mm, allowing for customization based on pressure needs. Thicker walls can withstand higher pressures, while thinner ones are suitable for less demanding, low-pressure applications.
- Length: Available in standard lengths such as 3000 mm, 6000 mm, and 12000 mm, with custom lengths also on offer to accommodate unique project layouts.
Monel 400 Wire & Mesh
For Monel 400 wire:
- Diameter: It typically ranges from 0.05 mm to 10 mm. Smaller diameters are perfect for intricate wiring tasks, like those in delicate electronic circuits, while larger diameters offer more strength for applications such as structural reinforcement.
- Length: Customizable lengths are available, starting from short lengths of 1 meter for small projects, up to several kilometers for large-scale industrial wiring needs.
Regarding Monel 400 mesh:
- Mesh Size: Options span from very fine, with openings as small as 0.01 mm, ideal for precise filtration, to coarser meshes with openings of up to 50 mm, which might be used for larger particle separation or protective screening.
- Sheet Size: Sheets of Monel 400 mesh can be supplied in standard sizes like 1000 mm x 1000 mm, and custom sizes are also offered to meet specific installation requirements.
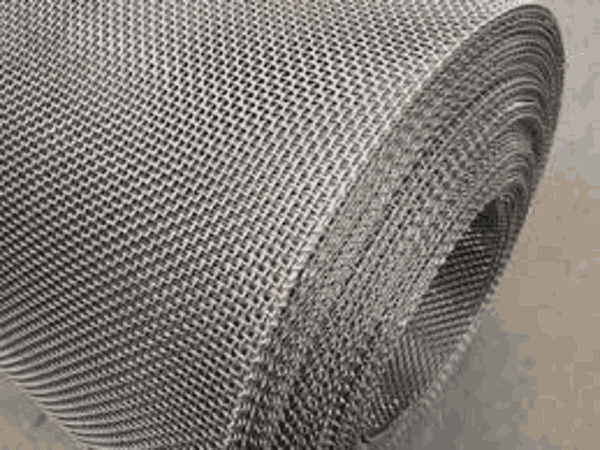
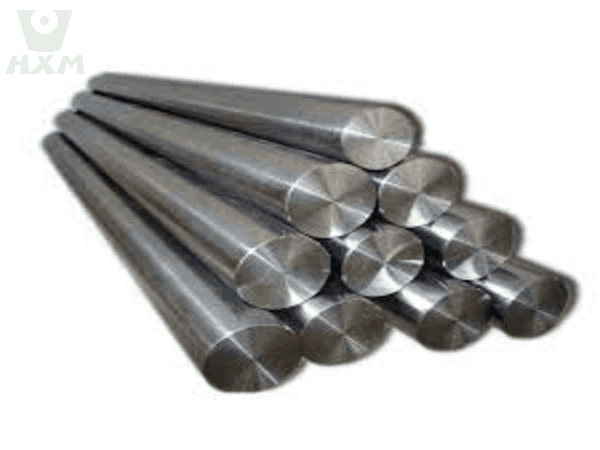
Monel 400 Bar
Dimensions:
- Diameter: It ranges from 3 mm to 300 mm. Smaller diameters are great for crafting precise, detailed parts, while larger diameters are for building more substantial, load-bearing structures.
- Length: Available in lengths from 1500 mm to 5000 mm, and we can also provide custom lengths according to the specific needs of your projects.
Monel Alloy 400 Chemical Composition
Element | Composition (wt.%) |
---|---|
Nickel (Ni) | 63.0 – 70.0 |
Copper (Cu) | 28.0 – 34.0 |
Iron (Fe) | 2.5 – 3.5 |
Manganese (Mn) | ≤ 2.0 |
Carbon (C) | ≤ 0.3 |
Silicon (Si) | ≤ 0.5 |
Sulfur (S) | ≤ 0.024 |
Phosphorus (P) | ≤ 0.02 |
Data Sheet
Physical Properties
Property | Value |
---|---|
Density | 8.83 g/cm³ 0.319 lb/in³ |
Melting Range | 2370 – 2460 °F 1300 – 1350 °C |
Modulus of Elasticity Tension | 26.0 x 10³ ksi |
Modulus of Elasticity Compression | 26.0 x 10³ ksi |
Modulus of Elasticity Torsion | 9.5 x 10³ ksi |
Poisson’s Ratio | 0.32 |
Curie Temperature | -195 – (-135) °F -125 – (-90) °C |
Thermal Conductivity | 21.8 W/m·K |
Specific Heat | 0.425 Btu/lb·°F |
Coefficient of Thermal Expansion (25 – 100°C) | 13.9 x 10⁻⁶ /°C |
Electrical Resistivity | 51.0 µΩ·cm |
mechanical properties
Form and Condition | Tensile Strength | Yield Strength (0.2% Offset) | Elongation, % | Hardness |
---|---|---|---|---|
Annealed | 65 – 85 ksi 448 – 586 MPa | 25 – 45 ksi 172 – 310 MPa | 35 – 50 | Brinell (3000-kg): 110 – 149 |
Cold-Worked (Drawn) | 80 – 110 ksi 552 – 758 MPa | 40 – 70 ksi 276 – 483 MPa | 20 – 35 | Brinell (3000-kg): 150 – 240 |
Hot-Finished | 70 – 95 ksi 483 – 655 MPa | 30 – 55 ksi 207 – 379 MPa | 30 – 45 | Brinell (3000-kg): 120 – 200 |
Welded (As-welded, Annealed) | 60 – 80 ksi 414 – 552 MPa | 20 – 40 ksi 138 – 276 MPa | 25 – 40 | Brinell (3000-kg): 100 – 170 |
Stress-Relieved | 75 – 105 ksi 517 – 724 MPa | 35 – 65 ksi 241 – 448 MPa | 30 – 45 | Brinell (3000-kg): 130 – 220 |
Monel 400 Introduction
Overview
Mechanical Properties
- Tensile Strength: Up to 85 ksi (586 MPa)
- Yield Strength (0.2% Offset): 25 – 45 ksi (172 – 310 MPa)
- Elongation: 35 – 50%
- Hardness: Brinell (3000-kg): 110 – 149
Corrosion Resistance
- Seawater Resistance: Monel 400 develops a protective film when exposed to seawater, thwarting rust and degradation over long periods.
- Acid Resistance: It demonstrates outstanding resistance to hydrofluoric acid, protecting equipment in chemical plants that handle this caustic substance.
- Alkaline Resistance: In alkaline environments, Monel 400 stays intact, preserving its structural integrity.
Density of Monel 400
Typical Applications
- Marine Equipment: For instance, ship fittings, propellers, and seawater piping systems, thanks to its excellent seawater corrosion resistance.
- Chemical Processing: Components in chemical reactors, valves, and pipes dealing with hydrofluoric acid or alkaline solutions.
- Oil & Gas: Parts for pumps, valves, and tubing in offshore oil platforms where corrosion from seawater and produced fluids is a worry.
- Electronics: Some electrical connectors profit from Monel 400’s corrosion resistance and dependable conductivity.
Monel 400 Applications
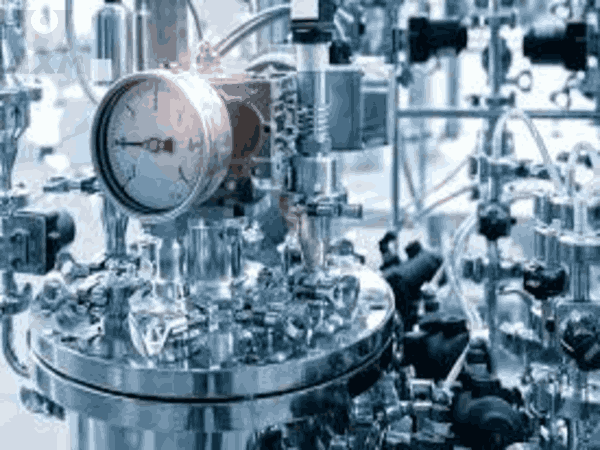
Marine Industry
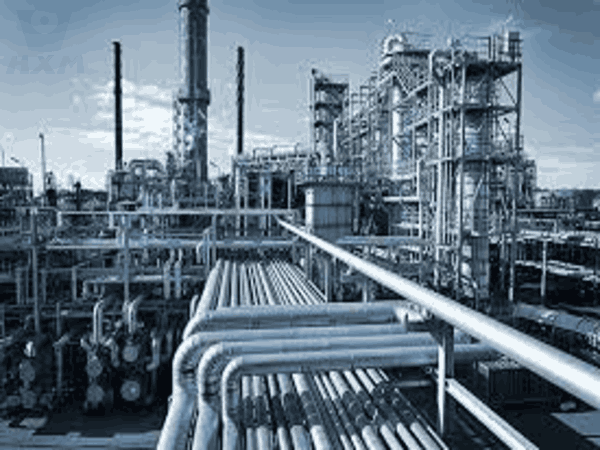
Chemical Processing
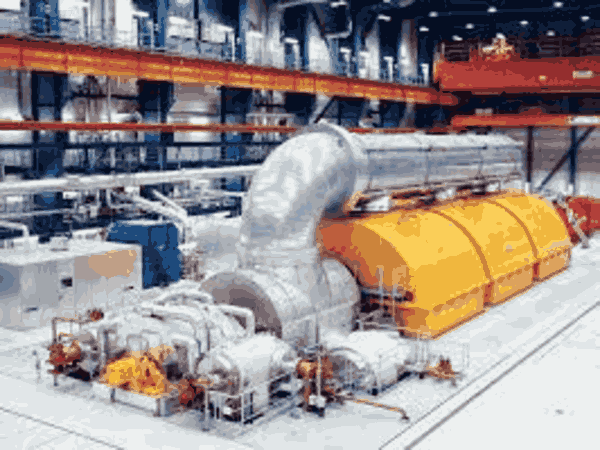
Nuclear Power Industry

Marine and Offshore Applications
FAQ
Monel 400 and K500 are both nickel – copper alloys. Monel 400 offers excellent corrosion resistance, especially to seawater and acids, and is cost-effective for general applications. Monel K500, on the other hand, undergoes precipitation hardening, giving it much higher strength. So, while 400 is ideal for corrosion-prone environments, K500 suits high-stress applications where strength matters more.
Monel 400 is a nickel-copper alloy with the UNS designation N04400. It’s highly regarded for its outstanding corrosion resistance, especially against seawater, hydrofluoric acid, and various alkaline solutions. This makes it a go-to material in industries such as marine engineering, chemical manufacturing, and oil & gas exploration. With good mechanical properties across a relatively wide temperature range, it can be easily fabricated into different forms like sheets, bars, pipes, and wires for diverse applications, from ship components to chemical reaction vessels.
More Incoloy Grades
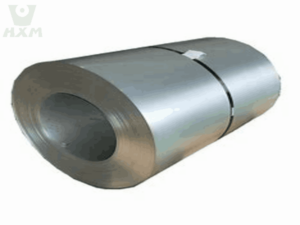
Monel Alloy 400
Previous slide Next slide Monel Alloy 400 Shapes: Plate & Sheet, Coil, Strip, Bar, Pipe & Tube, Wire & Mesh Grades: ASTM: B127 / UNS
Monel Alloy 404
Previous slide Next slide Monel Alloy 404 Shapes: Plate & Sheet,Coil,Strip,Bar,Pipe & Tube,Wire & Mesh Grades: ASTM: B[Relevant ASTM grade number for 404] / UNS
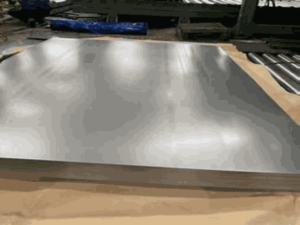
Monel Alloy 401
Previous slide Next slide Monel Alloy 401 Shapes: Plate & Sheet,Coil,Strip,Bar,Pipe & Tube,Wire & Mesh Grades: ASTM: [Relevant ASTM grade code for Monel 401] /