Incoloy 825 Alloy
Shapes:
Plate & Sheet, Coil, Strip, Bar, Pipe & Tube, Wire & Mesh
Grades:
ASTM: B424 / UNS N08825
ASME: SB424 / N08825
JIS: G4304 / SUS 825
AISI: 825
EN: 10088-2 / 1.4859
Huaxiao Metals is a trusted Incoloy 825 supplier, offering a wide range of high-quality Incoloy 825 products with competitive prices and exceptional services. We provide Incoloy 825, Incoloy 825H, and Incoloy 825HT in various specifications, lengths, and thicknesses. Each order undergoes a strict quality inspection and secure packaging to meet our customers’ precise requirements.
Contact Huaxiao Metals now for all your Incoloy 825 needs!
Incoloy Alloy 825 Shapes
Incoloy 825 Plate & Sheet
Incoloy 825 alloys are highly regarded for their superior resistance to corrosion, oxidation, and high-temperature strength, making them ideal for use in challenging industrial environments. With excellent resistance to acids like sulfuric acid, phosphoric acid, and seawater, Incoloy 825 is extensively used in industries such as chemical processing, marine, and oil & gas. Its remarkable mechanical properties and capability to perform in both high and low-temperature applications make Incoloy 825 an optimal choice for demanding performance applications.
Below are the dimensions for Incoloy 825 Plates & Sheets:
Dimensions:
Thickness: 0.3 mm – 200 mm
Width: 40 mm – 600 mm, 1000 mm, 1219 mm, 1500 mm, 1800 mm, 2000 mm, 2500 mm, 3000 mm, 3500 mm, and other custom widths available
Length: 2000 mm, 2500 mm, 3000 mm, 5800 mm, 6000 mm, 12000 mm, and other custom lengths available
For pricing, availability, and custom Incoloy 825 Plate & Sheet sizes, please contact us!
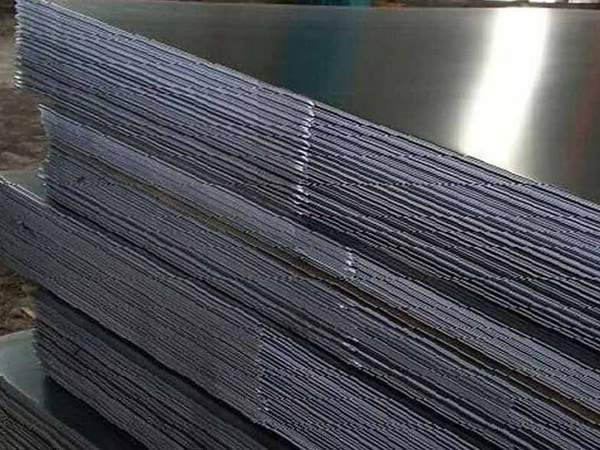
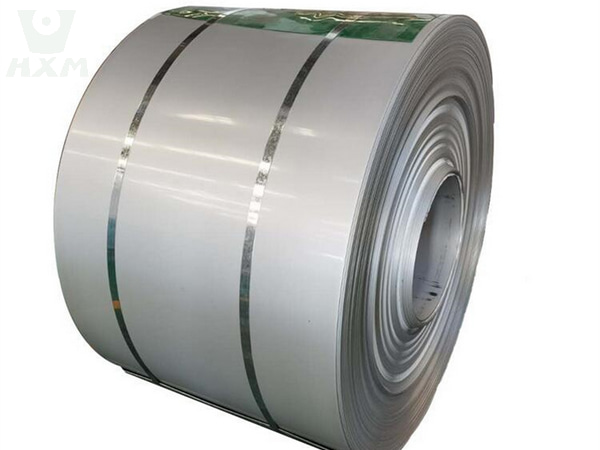
Incoloy 825 Coil
Incoloy 825 coils are highly sought after for their exceptional resistance to corrosion, oxidation, and high-temperature strength. These properties make Incoloy 825 an excellent choice for applications in harsh environments, such as chemical processing, marine, oil & gas, and pollution control. Incoloy 825’s outstanding resistance to acidic environments, including sulfuric acid, phosphoric acid, and seawater, combined with its excellent mechanical properties, make it a preferred material for a wide variety of industrial uses.
Dimensions of Incoloy 825 Coil:
- Thickness: 0.3 mm – 20 mm
- Width: 40 mm – 600 mm, 1000 mm, 1219 mm, 1500 mm, 1800 mm, 2000 mm, 2500 mm, 3000 mm, and other custom widths available
- Length: Coil lengths can be customized as per requirements
For pricing, availability, and custom Incoloy 825 Coil sizes, please contact us!
Incoloy 825 Strip
Incoloy 825 strips are widely used for their exceptional resistance to corrosion, oxidation, and high-temperature strength. This alloy offers outstanding performance in aggressive environments, including exposure to sulfuric acid, phosphoric acid, and seawater. The versatility of Incoloy 825 makes it a popular choice for industries such as chemical processing, marine, oil & gas, and pollution control, where material durability is essential in harsh operating conditions.
Below are the dimensions for Incoloy 825 Strips:
Dimensions:
- Thickness: 0.1 mm – 5 mm
- Width: 10 mm – 300 mm, 500 mm, 1000 mm, 1219 mm, and other custom widths available
- Length: Custom lengths available, based on specific requirements
For pricing, availability, and custom Incoloy 825 Strip sizes, please contact us!
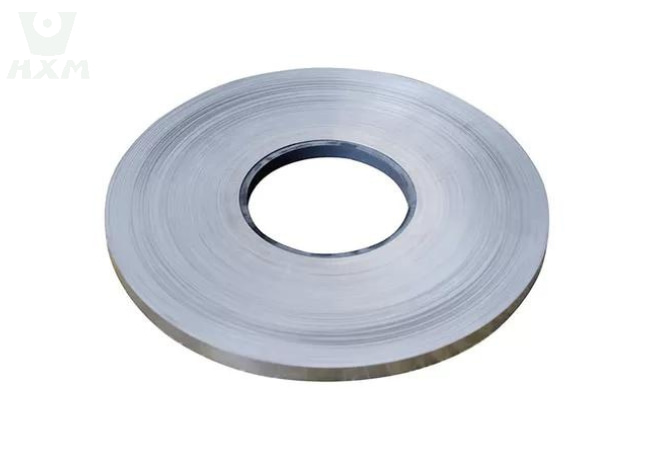
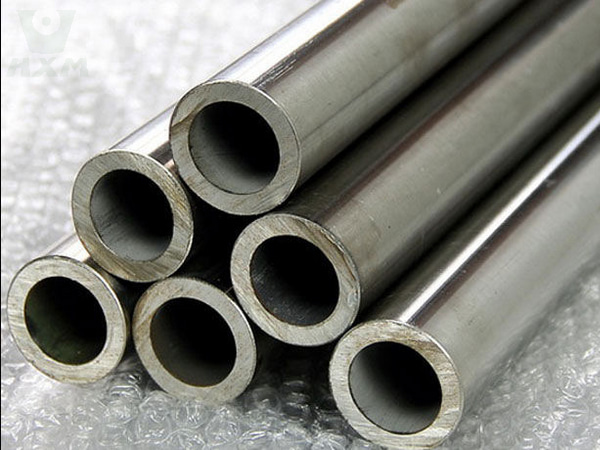
Incoloy 825 Pipe & Tube
Incoloy 825 pipes and tubes are highly valued for their outstanding resistance to corrosion, oxidation, and high-temperature strength. This alloy is ideal for applications in environments exposed to aggressive chemicals such as sulfuric acid, phosphoric acid, and seawater. Its excellent mechanical properties and versatility at both high and low temperatures make Incoloy 825 a preferred material in industries like chemical processing, marine, oil & gas, and pollution control.
Below are the dimensions for Incoloy 825 Pipes & Tubes:
Dimensions:
- Thickness: 0.5 mm – 50 mm
- Outer Diameter (OD): 10 mm – 1000 mm, and other custom sizes available
- Length: Custom lengths available based on specific requirements
For pricing, availability, and custom Incoloy 825 Pipe & Tube sizes, please contact us!
Incoloy 825 Wire & Mesh
Incoloy 825 wire and mesh are well-known for their excellent resistance to corrosion, oxidation, and high-temperature strength, making them ideal for use in aggressive environments. This alloy offers outstanding performance in chemical and marine industries, particularly in environments exposed to sulfuric acid, phosphoric acid, and seawater. Incoloy 825 wire and mesh are commonly used in applications such as filtration, heat exchangers, chemical reactors, and pollution control systems, where durability and resistance to corrosive substances are essential.
Below are the dimensions for Incoloy 825 Wire & Mesh:
Dimensions:
- Wire Diameter: 0.1 mm – 10 mm
- Mesh Size: Custom mesh sizes available based on requirements (e.g., 2 mesh to 200 mesh)
- Roll Length: Custom lengths available based on customer needs
For pricing, availability, and custom Incoloy 825 Wire & Mesh sizes, please contact us!
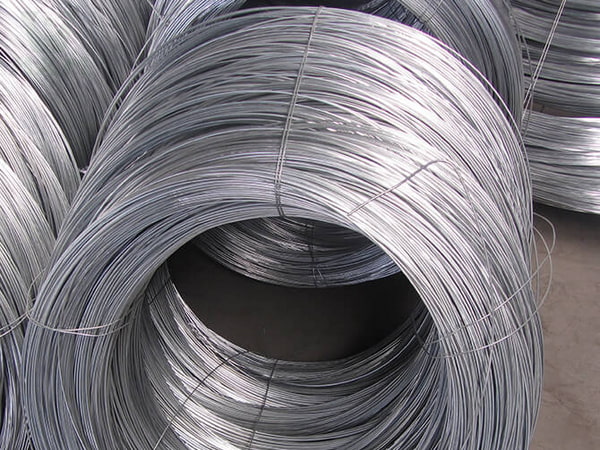
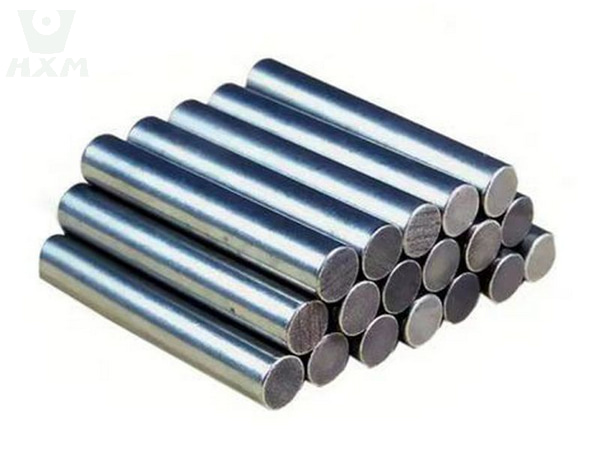
Incoloy 825 Bar
Incoloy 825 bars are widely used for their exceptional resistance to corrosion, oxidation, and high-temperature strength. This alloy is highly effective in environments where resistance to aggressive chemicals such as sulfuric acid, phosphoric acid, and seawater is required. The excellent mechanical properties and versatility of Incoloy 825 make it a preferred choice for applications in chemical processing, marine, oil & gas, and pollution control industries.
Below are the dimensions for Incoloy 825 Bars:
Dimensions:
- Diameter: 5 mm – 500 mm
- Length: Custom lengths available, typically ranging from 1000 mm to 6000 mm or as per customer specifications
- Finish: Cold Drawn, Hot Rolled, or Polished
For pricing, availability, and custom Incoloy 825 Bar sizes, please contact us!
Incoloy Alloy 825 Chemical Composition
Incoloy® 825 (UNS N08825) is a high-performance nickel-iron-chromium alloy known for its outstanding resistance to corrosion, oxidation, and high-temperature strength. This alloy is particularly effective in environments that are exposed to acidic environments, such as sulfuric acid, phosphoric acid, and seawater. It is commonly used in industries such as chemical processing, marine, oil & gas, and pollution control, where resistance to corrosion and high temperature performance are crucial. Below is the typical chemical composition of Incoloy 825:
Chemical Composition of Incoloy 825 (UNS N08825):
Element | Composition (wt.%) |
---|---|
Nickel (Ni) | 38.0 – 46.0 |
Iron (Fe) | Balance (approx. 22%) |
Chromium (Cr) | 19.5 – 23.5 |
Molybdenum (Mo) | 2.5 – 3.5 |
Copper (Cu) | 1.5 – 3.0 |
Titanium (Ti) | 0.60 – 1.20 |
Aluminum (Al) | 0.2 – 0.6 |
Carbon (C) | ≤ 0.05 |
Manganese (Mn) | ≤ 1.0 |
Silicon (Si) | ≤ 1.0 |
Sulfur (S) | ≤ 0.01 |
Phosphorus (P) | ≤ 0.03 |
Data Sheet
Physical Properties
Incoloy® 825 (UNS N08825) Properties
Property | Value |
---|---|
Density | 8.10 g/cm³ |
0.292 lb/in³ | |
Melting Range | 2460 – 2550 °F |
1350 – 1400 °C | |
Modulus of Elasticity | |
Tension | 28.0 x 10³ ksi |
Compression | 28.0 x 10³ ksi |
Torsion | 10.0 x 10³ ksi |
Poisson’s Ratio | 0.30 |
Curie Temperature | 660 – 800 °F |
350 – 425 °C | |
Thermal Conductivity | 10.6 W/m·K |
Specific Heat | 0.12 Btu/lb·°F |
Coefficient of Thermal Expansion (25-100°C) | 13.3 x 10⁻⁶ /°C |
Electrical Resistivity | 1.05 µΩ·cm |
Mechanical Properties
Incoloy® 825 (UNS N08825) Mechanical Properties
Form and Condition | Tensile Strength | Yield Strength (0.2% Offset) | Elongation, % | Hardness |
---|---|---|---|---|
Annealed (Solution Annealed) | 70-100 ksi | 30-60 ksi | 30-60 | Brinell (3000-kg): 207-414 |
483-690 MPa | 207-414 MPa | |||
Cold-Worked (Drawn) | 100-130 ksi | 35-55 ksi | 25-50 | Brinell (3000-kg): 241-448 |
690-896 MPa | 241-379 MPa | |||
Hot-Finished | 85-110 ksi | 35-60 ksi | 30-55 | Brinell (3000-kg): 207-414 |
586-758 MPa | 241-414 MPa | |||
Welded (As-welded, Annealed) | 70-90 ksi | 30-50 ksi | 20-45 | Brinell (3000-kg): 175-310 |
483-621 MPa | 207-345 MPa | |||
Heat-Exchanger Tubing (Annealed) | 75-100 ksi | 30-55 ksi | 25-50 | Brinell (3000-kg): 193-379 |
517-690 MPa | 207-379 MPa | |||
Stress-Relieved | 85-115 ksi | 40-70 ksi | 30-55 | Brinell (3000-kg): 241-448 |
586-793 MPa | 241-448 MPa |
These mechanical properties make Incoloy® 825 an ideal material for high-temperature and
Incoloy 825 Introduction
Overview
As a leading Incoloy 825 supplier, Oios Metals is committed to providing high-quality, cost-effective solutions for a range of industrial applications. Incoloy® 825 (UNS N08825) is a versatile nickel-iron-chromium alloy, highly valued for its excellent resistance to corrosion, oxidation, and sulfidation at elevated temperatures. This alloy is particularly effective in environments exposed to both high heat and aggressive chemicals, making it ideal for demanding industries such as chemical processing, petrochemical, marine, and power generation.
When comparing Incoloy 825 vs Inconel 825, Incoloy 825 stands out for its superior resistance to sulfuric acid, phosphoric acid, and seawater, as well as its ability to perform well under high temperatures. While Inconel 825 is preferred in more extreme high-temperature environments, Incoloy 825 provides a cost-effective solution for applications where corrosion resistance and high-temperature performance are paramount.
Mechanical Properties
Incoloy 825 is known for its outstanding mechanical properties, which help maintain performance in high-stress, high-temperature environments. The alloy retains its strength and creep resistance up to around 1100°F (593°C), making it ideal for applications in industries such as aerospace, petrochemical, and energy.
- Tensile Strength: Up to 100 ksi (690 MPa)
- Yield Strength (0.2% Offset): 35-55 ksi (241-379 MPa)
- Elongation: 25-50%
- Hardness: Brinell (3000-kg): 241-448
The excellent tensile strength and low thermal expansion of Incoloy 825 allow it to perform reliably in environments where both mechanical stress and temperature fluctuations are present.
Corrosion Resistance
One of the standout features of Incoloy 825 is its exceptional resistance to corrosion. This alloy performs excellently in environments that involve sulfuric acid, phosphoric acid, and seawater, making it highly suitable for chemical processing and petrochemical refining applications.
- Oxidation Resistance: Incoloy 825 provides outstanding protection against oxidation at elevated temperatures, ensuring durability in applications such as heat exchangers and furnace components.
- Corrosion Resistance: The alloy resists attack from sulfur-containing gases and acids, providing unmatched durability in aggressive environments.
- Sulfidation Resistance: It is particularly effective in resisting sulfidation, a key concern in many high-temperature industrial applications.
Additionally, Incoloy 825 demonstrates resistance to chloride stress corrosion cracking, making it an ideal choice for use in high-temperature, corrosive environments like industrial gas turbines and chemical reactors.
Density of Incoloy 825
The density of Incoloy 825 is approximately 8.00 g/cm³ (8000 kg/m³) at room temperature, which provides excellent strength and durability in high-temperature environments, enhancing the alloy’s performance under extreme conditions.
Typical Applications
- Heat exchangers and furnace components in the chemical and petrochemical industries
- Industrial gas turbines and combustion chambers
- Piping and furnace tubes in high-temperature environments
- Nuclear reactors and reactor components
- Heat treatment and thermal processing equipment
- Boilers and superheaters in power plants
Incoloy 825 is particularly well-suited for applications in industries where components are exposed to high temperatures and corrosive environments, including petrochemical refining, aerospace, and nuclear power.
Incoloy 825 Applications
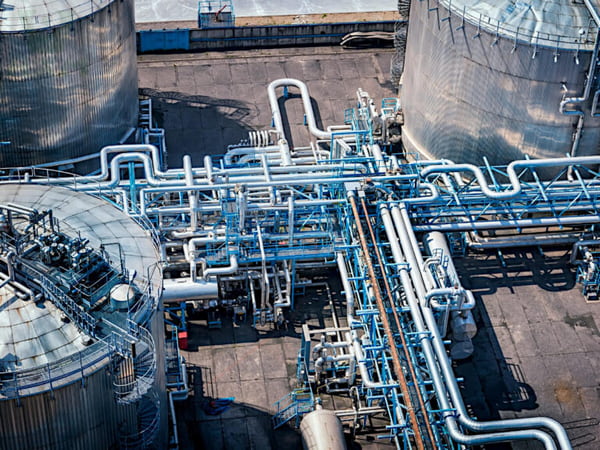
Chemical Processing
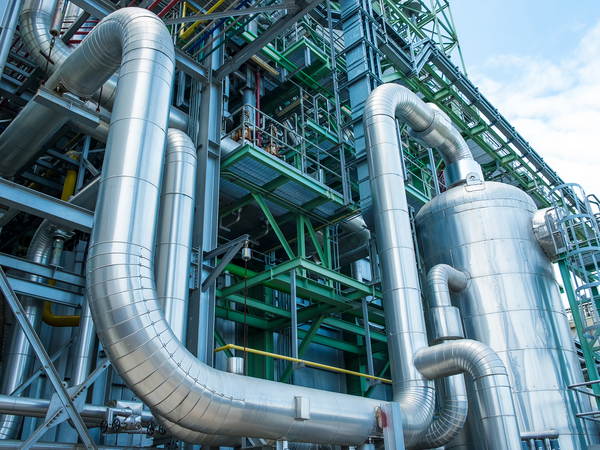
Petrochemical Refining
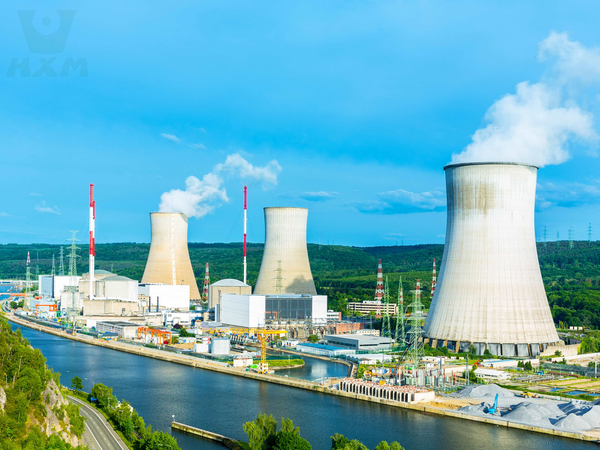
Nuclear Power Industry
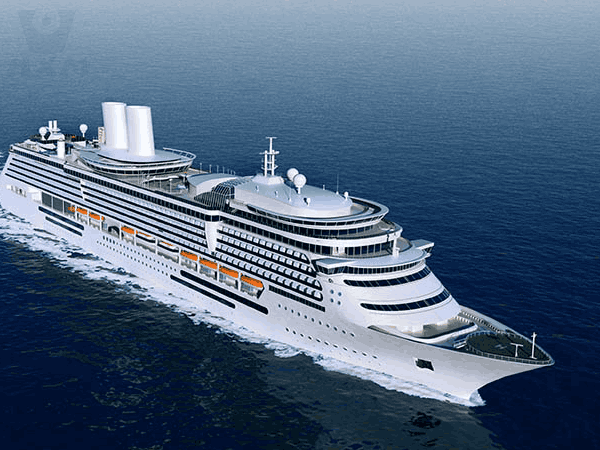
Marine and Offshore Applications
FAQ
what is the trade name for alloy 825?
What is difference between inconel 625 and incoloy 825
Inconel 625, with higher strength, has more nickel and niobium. In contrast, Incoloy 825, an iron-nickel-chromium alloy, offers good corrosion resistance in acidic media and is favored for chemical processing applications.
What is the difference between INCOLOY 825 and alloy 825?
There’s little practical difference; “INCOLOY 825” is a well-known trade name, while “alloy 825” is a more generic term, but they typically refer to the same nickel-iron-chromium alloy with similar properties.
More Incoloy Grades
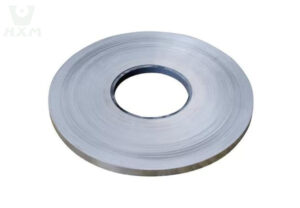
Incoloy Alloy 825
Previous slide Next slide Incoloy 825 Alloy Shapes: Plate & Sheet, Coil, Strip, Bar, Pipe & Tube, Wire & Mesh Grades: ASTM: B424 / UNS
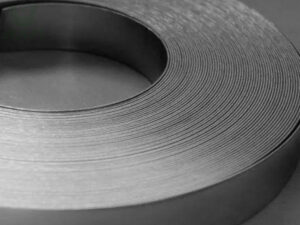
Incoloy Alloy 803
Previous slide Next slide Incoloy Alloy 803 Shapes: Plate & Sheet, Coil, Strip, Bar, Pipe & Tube, Wire & Mesh Grades: ASTM: A240 / S80300
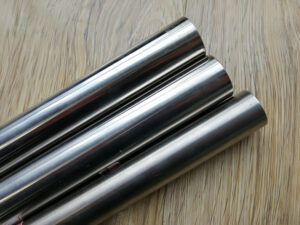
Incoloy Alloy 800
Previous slide Next slide Incoloy Alloy 800 Shapes: Plate & Sheet,Coil,Strip,Bar,Pipe & Tube,Wire & Mesh Grades: ASTM: A240 / S80000, S800H, S800HTJIS: G4304 / SUS800,