Incoloy Alloy 800
Shapes:
Plate & Sheet,Coil,Strip,Bar,Pipe & Tube,Wire & Mesh
Grades:
ASTM: A240 / S80000, S800H, S800HT
JIS: G4304 / SUS800, SUS800H, SUS800HT
AISI: 800, 800H, 800HT
EN: 10088-2 / 1.4876, 1.4859, 1.4858
Mill’s Standard: 800, 800H, 800HT
Huaxiao Metal is a leading Incoloy Alloy 800 supplier, offering the best prices and services. We provide Incoloy 800, Incoloy 800H, and Incoloy 800HT products in any specification, length, and thickness. Each order undergoes strict quality inspection and careful packaging to meet customer requirements.Contact us now!
Incoloy Alloy 800 Shapes
Incoloy 803 Plate & Sheet
Incoloy 803 alloys are highly valued for their outstanding resistance to oxidation, carburization, and excellent high-temperature strength. These properties make Incoloy Alloy 803 an ideal material for a wide range of industrial applications, especially in high-temperature environments. Below are the dimensions for Incoloy 803 Plates & Sheets:
Dimensions:
- Thickness: 0.3 mm – 200 mm
- Width: 40 mm – 600 mm, 1000 mm, 1219 mm, 1500 mm, 1800 mm, 2000 mm, 2500 mm, 3000 mm, 3500 mm, and other custom widths of Incoloy 803 available
- Length: 2000 mm, 2500 mm, 3000 mm, 5800 mm, 6000 mm, 12000 mm, and other custom lengths for Incoloy Alloy 803
For pricing, availability, and custom Incoloy 803 Plate & Sheet sizes, please contact us!
As a trusted Incoloy Alloy 803 supplier, Huaxiao Metals offers high-quality Incoloy 803 products. Whether you’re comparing Incoloy vs Inconel, looking for reliable Incoloy material solutions, or need custom Incoloy 803 specifications, we provide the best options tailored to your needs.

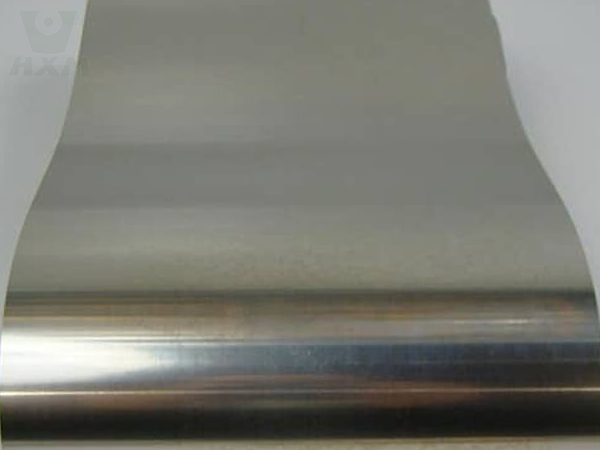
Incoloy 800 Coil
Incoloy 800 coils are known for their outstanding resistance to oxidation and carburization at high temperatures, making them ideal for high-temperature industrial applications. These coils offer excellent strength and reliability, particularly in environments that involve elevated heat. Below are the dimensions for Incoloy 800 Coils:
Dimensions:
- Thickness: 0.3 mm – 10 mm
- Width: 40 mm – 600 mm, 1000 mm, 1219 mm, 1500 mm, 1800 mm, 2000 mm, 2500 mm, 3000 mm, and other custom widths of Incoloy 800 available
- Length: Customizable, available in coils or specific lengths based on customer requirements
For pricing, availability, and custom Incoloy 800 coil sizes, feel free to contact us!
Incoloy 800 Strip
Incoloy 800 strips offer excellent resistance to oxidation, carburization, and high-temperature strength, making them ideal for a wide range of industrial applications. These strips are designed to perform reliably in high-temperature environments, ensuring durability and longevity in critical applications. Below are the dimensions for Incoloy 800 Strips:
Dimensions:
- Thickness: 0.3 mm – 5 mm
- Width: 40 mm – 600 mm, 1000 mm, 1219 mm, 1500 mm, 1800 mm, 2000 mm, 2500 mm, 3000 mm, and other custom widths of Incoloy 800 available
- Length: Customizable, available in rolls or specific lengths as per customer requirements
For pricing, availability, and custom Incoloy 800 strip sizes, please contact us!
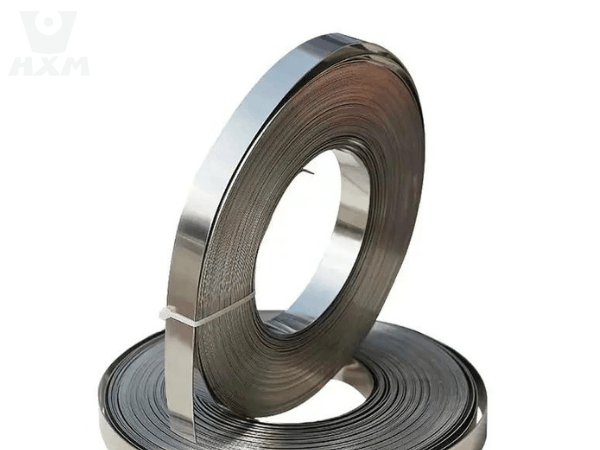
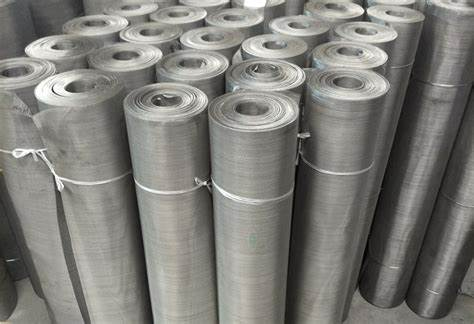
Incoloy 800 Pipe & Tube
Incoloy 800 pipes and tubes offer exceptional resistance to oxidation, carburization, and high-temperature strength, making them ideal for demanding applications such as heat exchangers, nuclear reactors, and other high-temperature environments. These materials are designed to withstand extreme conditions while maintaining their mechanical properties. Below are the dimensions for Incoloy Alloy Pipes & Tubes:
Dimensions:
Pipe:
- Thickness: 1 mm – 50 mm
- Outer Diameter (OD): 15 mm – 500 mm (Custom sizes available)
- Length: 2000 mm, 2500 mm, 3000 mm, 5800 mm, 6000 mm, 12000 mm, and other custom lengths available
Tube:
- Wall Thickness: 0.3 mm – 25 mm
- Outer Diameter (OD): 6 mm – 350 mm (Custom sizes available)
- Length: Custom lengths available upon request
For pricing, availability, and custom Incoloy 800 pipe & tube sizes, feel free to contact us!
Incoloy 800 Wire & Mesh
Incoloy 800 wire and mesh are renowned for their exceptional resistance to oxidation, carburization, and high-temperature strength, making them ideal for high-temperature environments, chemical processing, and heat exchangers. These materials are designed to perform reliably in harsh conditions, ensuring long-term durability and performance. Below are the dimensions for Incoloy Alloy Wire & Mesh:
Dimensions:
Wire:
- Diameter: 0.1 mm – 10 mm (Custom sizes available)
- Length: Custom lengths or coils available upon request
Mesh:
- Mesh Size: 0.5 mm – 25 mm (Custom sizes available)
- Thickness: 0.1 mm – 5 mm
- Width: 100 mm – 1500 mm (Custom widths available)
- Length: Customizable to suit specific project requirements
For pricing and custom wire & mesh sizes, please contact us!
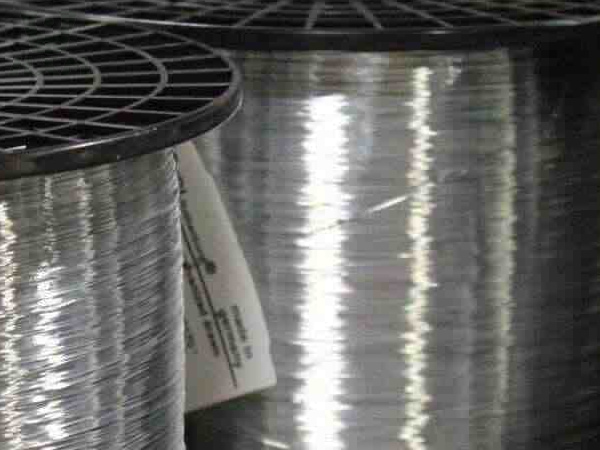
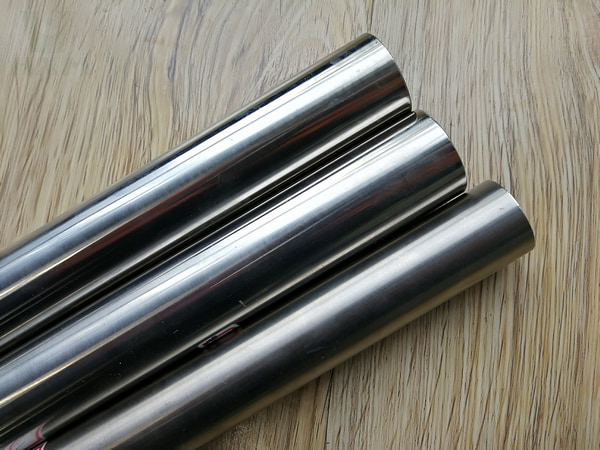
Incoloy 800 Bar
Incoloy 800 bars are known for their excellent resistance to oxidation, carburization, and high-temperature strength, making them highly suitable for use in furnace components, heat exchangers, and chemical processing equipment. These bars offer exceptional performance in harsh environments where high temperature and chemical resistance are required. Below are the dimensions for Incoloy 800 Bar:
Dimensions:
Bar:
- Diameter: 5 mm – 500 mm (Custom sizes available)
- Length: Custom lengths or cut-to-size bars available upon request
For pricing and custom bar sizes, please contact us!
Incoloy Alloy 800 Chemical Composition
Incoloy® 800 (UNS N08800) is a nickel-iron-chromium alloy with the following typical chemical composition:
Element | Composition (wt.%) |
---|---|
Nickel (Ni) | 30.0 – 35.0 |
Iron (Fe) | Balance (approximately) |
Chromium (Cr) | 19.0 – 23.0 |
Carbon (C) | ≤ 0.10 |
Manganese (Mn) | ≤ 1.50 |
Silicon (Si) | ≤ 1.00 |
Sulfur (S) | ≤ 0.015 |
Copper (Cu) | ≤ 0.75 |
Aluminum (Al) | ≤ 1.00 |
Titanium (Ti) | 0.15 – 0.60 |
Phosphorus (P) | ≤ 0.015 |
Data Sheet
Physical Properties
Property | Value |
---|---|
Density | 8.00 g/cm³ |
0.289 lb/in³ | |
Melting Range | 2460 – 2550 °F |
1350 – 1400 °C | |
Modulus of Elasticity | |
Tension | 28.0 x 10³ ksi |
Compression | 28.0 x 10³ ksi |
Torsion | 10.0 x 10³ ksi |
Poisson’s Ratio | 0.31 |
Curie Temperature | 660 – 800 °F |
350 – 425 °C |
Mechanical Properties
Form and Condition | Tensile Strength | Yield Strength (0.2% Offset) | Elongation, % | Hardness |
---|---|---|---|---|
ksi | MPa | ksi | MPa | Brinell (3000-kg) |
————————————- | ———————- | ——————————— | ——————- | ———————— |
Annealed (Solution Annealed) | 70-100 | 483-690 | 30-60 | 207-414 |
Cold-Worked (Drawn) | 100-130 | 690-896 | 35-55 | 241-448 |
Hot-Finished | 85-110 | 586-758 | 35-60 | 207-414 |
Welded (as-welded, annealed) | 70-90 | 483-621 | 30-50 | 175-310 |
Heat-Exchanger Tubing (Annealed) | 75-100 | 517-690 | 30-55 | 193-379 |
Stress-Relieved | 85-115 | 586-793 | 40-70 | 241-448 |
Incoloy 800 Introduction
Overview
As a leading Incoloy Alloy 800 supplier in China, AEETHER provides cost-effective Incoloy® 800 products for a variety of industrial applications.
Incoloy® 800 (UNS N08800 / W.Nr. 1.4876) is a solid-solution nickel-iron-chromium alloy known for its exceptional resistance to oxidation and carburization at elevated temperatures. It combines the high-temperature strength of austenitic alloys with excellent resistance to oxidation, sulfidation, and carburization. Incoloy 800, Incoloy 800H, and Incoloy 800HT are ideal materials for use in harsh, high-temperature environments, particularly within the chemical and petrochemical industries.
Incoloy 800 is widely used in heat exchangers, furnace components, nuclear reactors, and other applications that demand high strength and resistance to oxidation at high temperatures. It is also frequently used in thermal processing equipment, such as in the production of heat exchangers, piping, and combustion chambers.
Mechanical Properties
Incoloy Alloy 800 offers outstanding mechanical properties at high temperatures, making it suitable for applications that experience both mechanical stress and elevated temperatures. The alloy maintains good tensile strength and creep resistance up to approximately 1100°F (593°C).
At high temperatures, Incoloy 800H and Incoloy 800 exhibit excellent strength, toughness, and low thermal expansion rates. These alloys also show great resistance to thermal fatigue, making them ideal for use in demanding high-temperature environments. Incoloy 800HT is specifically designed to retain its mechanical properties even under extreme heat, ensuring long-term performance in harsh conditions.
Corrosion Resistance
Incoloy 800 is highly resistant to both oxidation and carburization, particularly in high-temperature environments. This superior corrosion resistance makes Incoloy 800 ideal for furnace and combustion applications where exposure to high heat and aggressive chemical conditions is common.
The alloy also demonstrates exceptional resistance to many forms of sulfuric acid and chloride stress cracking, offering reliable performance in high-temperature and chemically aggressive environments. Incoloy 800H is especially resistant to corrosion in both carburizing and oxidizing atmospheres, making it a popular choice in petrochemical refining processes and similar high-temperature applications.
- Oxidation Resistance: Incoloy 800 provides outstanding protection against oxidation at elevated temperatures, making it a preferred material for furnace components and high-heat environments.
- Corrosion Resistance: The alloy exhibits remarkable resistance to sulfur-containing gases and acids, particularly at high temperatures, and is also highly resistant to aqueous corrosion in a variety of chemical environments.
Density of Incoloy 800
The density of Incoloy 800 is approximately 7.94 g/cm³ (7940 kg/m³) at room temperature. This makes it a relatively dense alloy, suitable for applications where strength and durability are critical in high-temperature conditions.
Typical Applications
- Heat exchangers and furnace components in the chemical and petrochemical industries
- Nuclear reactors and reactor components
- Industrial gas turbines and combustion chambers
- Piping and furnace tubes exposed to high temperatures
- Heat treatment and thermal processing equipment
- Boilers and superheaters in power plants
- Chemical processing systems operating at elevated temperatures
Incoloy 800, Incoloy 800H, and Incoloy 800HT are selected for their ability to withstand extreme conditions, ensuring long-term reliability and performance in high-temperature environments across a broad range of industries.
For more information on Incoloy 800 chemical composition, Incoloy 800 ASTM specification, Incoloy 800 specification, Incoloy 800 equivalent materials, and Incoloy 800 welding procedures, please contact us for expert guidance.
Incoloy 800 Applications
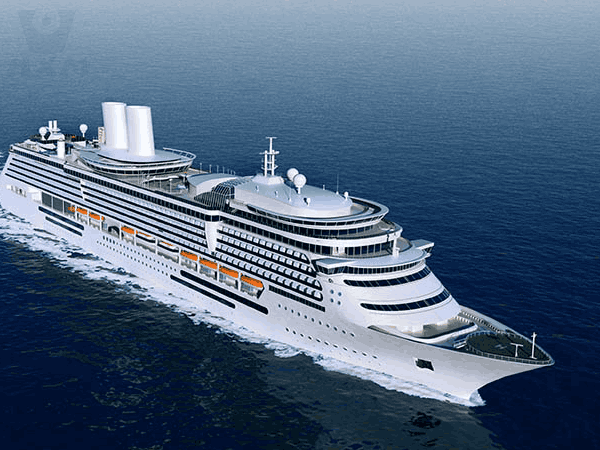
Marine Applications
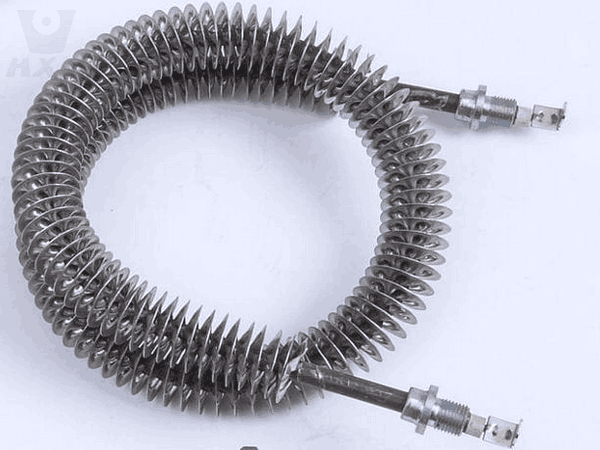
Heating Elements
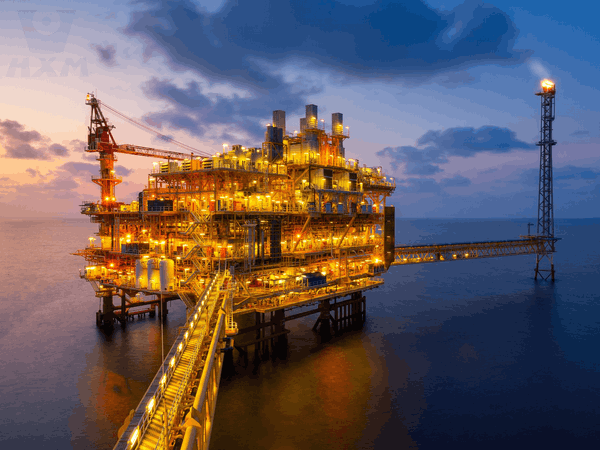
Oil and Gas Industry
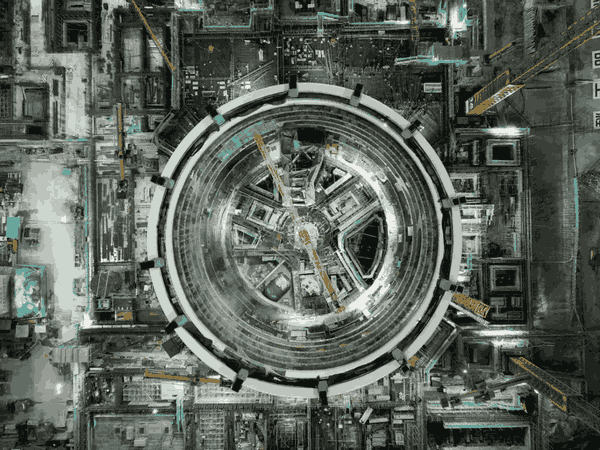
Nuclear Industry
FAQ
What is the difference between Inconel 800 and INCOLOY 800?
What is the equivalent of INCOLOY 800?
The equivalent of INCOLOY 800 includes materials like UNS N08800. It is a nickel-iron-chromium alloy, and similar alloys from other manufacturers might also serve as equivalents, often sharing comparable corrosion resistance, high-temperature strength, and mechanical properties for use in heat exchanger, furnace components, and chemical processing applications.
What is INCOLOY 800 material?
Incoloy 800 is a nickel-chromium-iron alloy known for its excellent resistance to oxidation and carburization at high temperatures. It is commonly used in high-temperature applications like heat exchangers, furnace components, and chemical processing.
800 vs 800ht?
- Composition differences: Chemically, Incoloy 800HT has slightly higher contents of carbon, aluminum, and titanium compared to 800. These elemental adjustments enhance its high-temperature performance.
- Temperature resistance: Incoloy 800HT can withstand higher temperatures, with an upper service limit of around 1100 °C, while Incoloy 800 has a maximum service temperature of approximately 950 °C.
- Application scenarios: Incoloy 800 is commonly used in general high-temperature chemical and energy recovery devices with certain corrosion conditions. In contrast, 800HT is suitable for petrochemical cracking, nuclear reactor internals, and other extremely high-temperature and severely stressed environments.
More Incoloy Grades
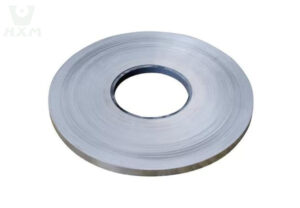
Incoloy Alloy 825
Previous slide Next slide Incoloy 825 Alloy Shapes: Plate & Sheet, Coil, Strip, Bar, Pipe & Tube, Wire & Mesh Grades: ASTM: B424 / UNS
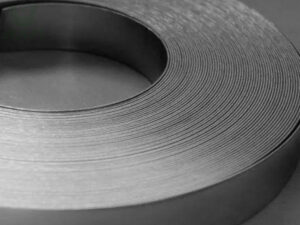
Incoloy Alloy 803
Previous slide Next slide Incoloy Alloy 803 Shapes: Plate & Sheet, Coil, Strip, Bar, Pipe & Tube, Wire & Mesh Grades: ASTM: A240 / S80300
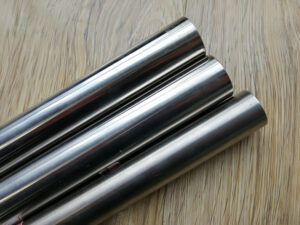
Incoloy Alloy 800
Previous slide Next slide Incoloy Alloy 800 Shapes: Plate & Sheet,Coil,Strip,Bar,Pipe & Tube,Wire & Mesh Grades: ASTM: A240 / S80000, S800H, S800HTJIS: G4304 / SUS800,