Huaxiao Metal – A Top Inconel Alloy Manufacturer in China
Huaxiao Metal is a leading Inconel alloy supplier in China, offering a wide range of high-performance Inconel alloys including Inconel 625, Inconel 718, Inconel 825, Inconel 601, Inconel 625 alloy composition, Inconel 718 alloy composition, Inconel alloy 22, Inconel alloy 601, Inconel alloy 617, Inconel alloy 690, Inconel alloy 718, Inconel alloy 725, Inconel alloy C-276, Inconel alloy HX, Inconel alloy X750, and many more. As a trusted Inconel alloy supplier, we are committed to providing only the highest-quality materials for demanding industrial applications.
Our Inconel alloys are well-known for their exceptional resistance to high-temperature oxidation, corrosion, and their outstanding mechanical properties, making them perfect for industries like aerospace, chemical processing, petrochemical, and power generation. Whether you’re in need of Inconel 625, Inconel 718 nickel alloy, Inconel 800, or Inconel alloy 825, we offer a broad selection of alloys to meet your specific requirements.
As a leading Inconel alloy supplier, we specialize in providing Inconel alloys like Inconel 100 alloy, Inconel alloy C276, Inconel alloy X750, and Inconel 625 alloy with unmatched strength and durability. Our products are ideal for extreme environments, offering superior performance in heat exchangers, gas turbines, reactors, and more.
With a wide range of high-performance Inconel alloys in stock and competitive prices, we ensure reliable delivery and tailored solutions to meet your business’s needs. As a trusted Inconel alloy supplier, we guarantee our products will exceed your expectations in the most demanding applications. Contact us today to explore our selection of Inconel alloys and find the right material for your industrial requirements.
Inconel Alloy Products
Inconel Alloy 617
Inconel Alloy 617 Inconel Alloy 617: High-Performance Nickel-Chromium Alloy for Extreme Environments Inconel Alloy 617 is a high-temperature, oxidation-resistant nickel-chromium-cobalt alloy designed for service in
Inconel Alloy 601
Inconel Alloy 601 Inconel Alloy 601: High-Temperature Nickel-Chromium Alloy with Superior Oxidation and Corrosion Resistance Inconel Alloy 601 is a high-performance nickel-chromium-based alloy known
Inconel Alloy 600
Previous slide Next slide Inconel 600 Alloy Shapes: Plate & Sheet, Coil, Strip, Bar, Pipe & Tube, Wire & Mesh Grades: ASTM: B127 / UNS
Inconel Alloy Classification
Classification of Inconel Alloys:
Inconel alloys are available in various grades, each designed to meet the performance requirements of demanding industrial applications. As a trusted Inconel alloy supplier, we offer a broad range of alloys, including Inconel 625, Inconel 718, Inconel 825, Inconel 601, Inconel alloy 22, Inconel alloy 617, Inconel alloy 625, Inconel alloy 690, Inconel alloy 718, Inconel alloy 725, Inconel alloy C-276, Inconel alloy HX, Inconel alloy X750, Inconel alloy 800, and more. Some of the most commonly used Inconel alloys we supply include:
Inconel 625: Known for its excellent resistance to oxidation and corrosion, particularly in high-temperature environments, Inconel 625 is ideal for applications in aerospace, marine, and chemical processing industries. As leading Inconel alloy 625 suppliers, we provide this alloy for industries requiring high-performance materials.
Inconel 718: This high-strength, heat-resistant alloy is widely used in the aerospace and power generation sectors. With its excellent creep and oxidation resistance, Inconel 718 is perfect for turbine blades, reactors, and other high-temperature applications. As a reliable Inconel alloy 718 supplier, we offer this alloy for the most demanding environments.
Inconel 825: Known for its superior resistance to corrosion, Inconel 825 is widely used in chemical processing, nuclear industries, and marine applications. As a trusted supplier of Inconel alloy 825, we ensure that our products provide outstanding resistance to acids, chlorides, and other harsh environments.
Inconel alloy 601: This alloy is designed for excellent oxidation and carburization resistance at elevated temperatures, making it suitable for applications such as gas turbines, heat exchangers, and industrial furnaces. We provide Inconel alloy 601 to meet the high-performance needs of these sectors.
Inconel alloy 625: This alloy features high resistance to extreme environments, including high-temperature oxidation, carburization, and corrosion. As an experienced Inconel 625 alloy supplier, we offer solutions for applications in aerospace, chemical processing, and marine industries.
Inconel alloy 718: Featuring a unique composition of nickel-chromium, Inconel alloy 718 offers remarkable strength and excellent weldability at high temperatures. It’s commonly used in the aerospace and power generation industries. As an Inconel alloy 718 supplier, we ensure superior quality and reliability.
Inconel alloy 690: Known for its high resistance to stress corrosion cracking, Inconel 690 is commonly used in heat exchangers, reactors, and other industrial equipment exposed to high-temperature environments. As a trusted supplier, we offer Inconel alloy 690 for demanding applications.
Inconel C-276: Inconel C-276 is highly resistant to a wide range of corrosive environments, including sulfuric acid, phosphoric acid, and chlorides. This alloy is used in chemical processing and marine industries, and we supply this alloy to meet the specific needs of these sectors.
Inconel alloy X750: Inconel X750 is used in high-temperature applications such as gas turbines and reactors, thanks to its excellent creep and oxidation resistance. As a leading Inconel alloy X750 supplier, we offer this alloy for applications where strength and reliability are essential.
Inconel 800: Inconel 800 offers excellent oxidation and carburization resistance at elevated temperatures. It is commonly used in heat exchangers, boilers, and other high-temperature applications. We supply Inconel 800 to ensure outstanding performance in these demanding environments.
As an established Inconel alloy supplier, we offer tailored solutions to meet the needs of various industries, including aerospace, chemical processing, petrochemical, and power generation. Whether you’re looking for Inconel 625, Inconel 718, Inconel alloy 825, or other Inconel alloys, we provide high-quality products with excellent performance in the most challenging environments. Contact us today to learn more about our selection of Inconel alloys and find the right material for your application at competitive prices.
1.Inconel 600
Composition:
Nickel (72-78%), Chromium (14-17%), Iron (6-10%), Manganese (max 1%), Silicon (max 0.5%), Carbon (max 0.15%), Sulfur (max 0.015%).
Properties:
Excellent oxidation and corrosion resistance at high temperatures. High strength and resistance to thermal fatigue and thermal shock. Good weldability and formability. Resistant to sulfur-containing gases, carburizing environments, and chlorine.
Applications:
Used in high-temperature applications such as gas turbines, heat exchangers, furnace components, and chemical processing equipment. Commonly found in the aerospace, power generation, and nuclear industries. Ideal for environments where high resistance to oxidation and carburization is critical.
2.Inconel 601
Composition:
Nickel (58-63%), Chromium (21-25%), Iron (14-18%), Manganese (max 1.0%), Silicon (1.0-1.7%), Carbon (max 0.10%), Sulfur (max 0.015%), Aluminum (0.4-1.0%).
Properties:
Excellent resistance to oxidation and carburization at high temperatures. Outstanding resistance to heat, scaling, and thermal cycling. Good resistance to sulfur-containing gases and chloride environments. High strength and good weldability. Superior performance in both oxidation and corrosive environments at elevated temperatures.
Applications:
Used in high-temperature applications such as industrial furnaces, heat treatment processes, gas turbines, and chemical processing equipment. Also applied in the aerospace industry, power plants, and pollution control systems where high resistance to oxidation and thermal degradation is essential. Ideal for components exposed to elevated temperatures and aggressive environments.
3.Inconel 617
Composition:
Nickel (50-60%), Chromium (20-23%), Cobalt (12-15%), Molybdenum (8-10%), Iron (max 10%), Aluminum (1.0-1.5%), Tantalum (max 1%), Carbon (max 0.1%), Silicon (max 0.5%), Manganese (max 1%).
Properties:
Excellent oxidation and corrosion resistance at very high temperatures, up to 2200°F (1200°C). Outstanding resistance to both sulfur and chlorine-containing environments. High strength and good creep resistance at elevated temperatures. Good weldability and formability. Strong resistance to thermal cycling and spalling.
Applications:
Commonly used in high-temperature applications such as gas turbines, jet engines, and combustion chambers. Ideal for components in the chemical processing, power generation, and aerospace industries. Also employed in heat exchangers, reactor cores, and other systems exposed to severe high-temperature environments with aggressive gaseous conditions.
Inconel Alloy Advantages
Applications of Inconel Alloy
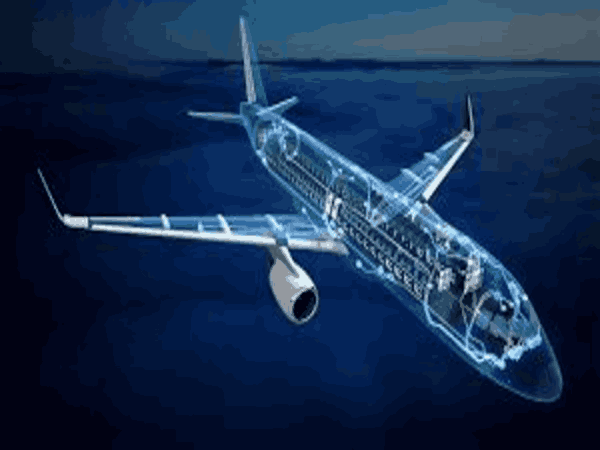
Aerospace and Aviation
Inconel alloys are ideal for aerospace and aviation components, including turbine blades, exhaust systems, and combustion chambers, offering high-temperature strength, excellent oxidation resistance, and durability under thermal cycling.
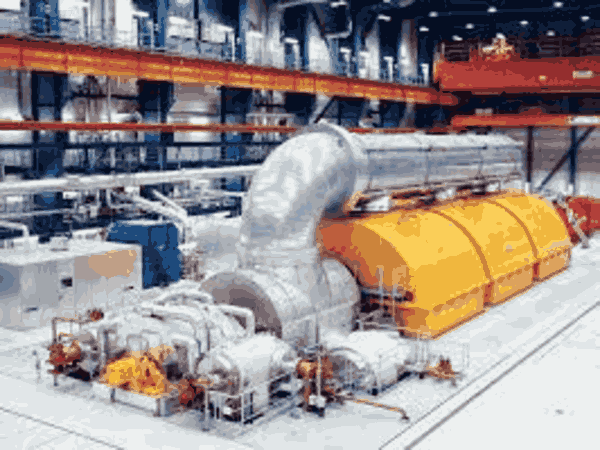
Power Generation
Inconel alloys are ideal for power generation components such as gas turbine blades, steam turbines, and heat exchangers, providing high-temperature strength, resistance to oxidation and corrosion, and excellent durability in harsh, high-stress environments.
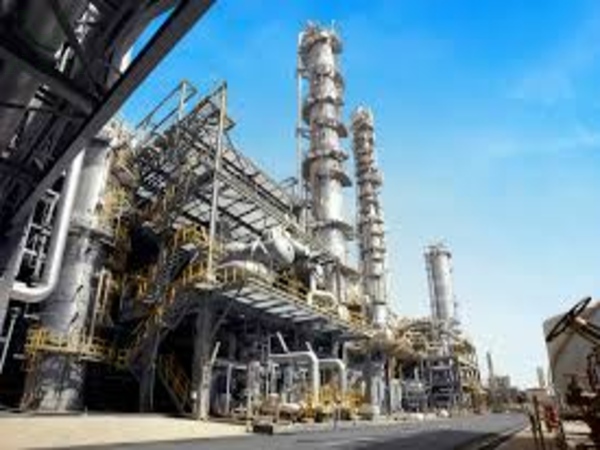
Chemical Processing
Inconel alloys are ideal for chemical processing components like reactors, heat exchangers, and furnace parts, offering excellent resistance to high-temperature corrosion, oxidation, and aggressive chemicals, ensuring reliable performance in harsh environments.

Marine and Offshore Applications
Inconel alloys are used in marine and offshore applications for their excellent resistance to corrosion, oxidation, and high-temperature environments, making them ideal for components like turbine blades, seawater piping, and heat exchangers.
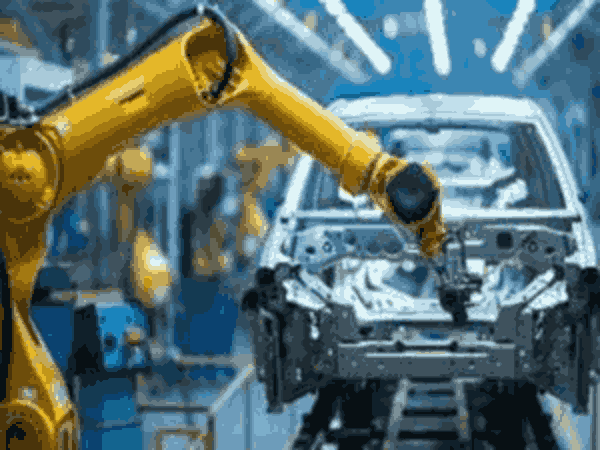
Automotive and Racing
Inconel alloys are ideal for automotive and racing components, such as turbochargers, exhaust systems, and engine parts, offering exceptional heat resistance, high strength, and durability under extreme thermal cycling and high-performance conditions.
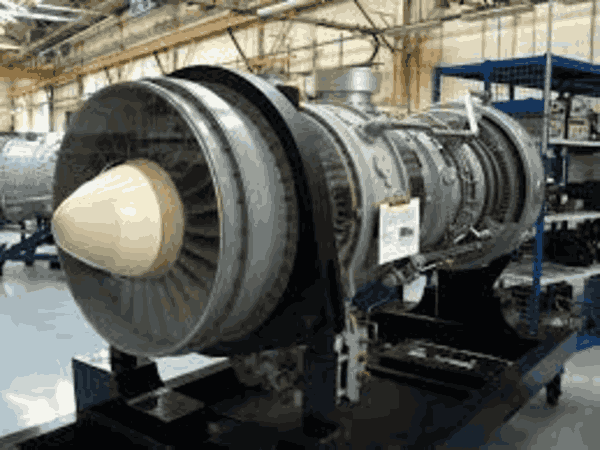
Marine Gas Turbines
Inconel alloys are ideal for marine gas turbines, including turbine blades and combustion chambers, providing excellent resistance to high temperatures, oxidation, and corrosion in the harsh, saltwater environment commonly found in naval and offshore power generation applications.
If you are unsure about the applications of Inconel alloys in various industries, you can contact us, Inconel alloy supplier, to learn more.
FAQ
1. Alloy 825 vs Inconel 625?
Alloy 825 is better for moderate temperature and corrosive environments, while Inconel 625 excels in high-temperature strength and oxidation resistance.
2. Inconel vs Hastelloy?
Inconel is better for high-temperature strength and oxidation resistance, while Hastelloy excels in resisting corrosion, particularly in harsh chemical environments.
3. What does Inconel Nickel Alloy contain?
Inconel nickel alloys primarily contain nickel (50-75%) and chromium (up to 30%), with additions of iron, molybdenum, niobium, and titanium for enhanced strength, oxidation, and corrosion resistance at high temperatures.
4. Machining Inconel 718 Alloy?
Machining Inconel 718 alloy is challenging due to its high strength and toughness at elevated temperatures. It requires the use of sharp tools, low cutting speeds, and frequent coolant application to prevent heat buildup and tool wear. Specialized techniques like electrical discharge machining (EDM) and precision grinding are often used for intricate shapes.
5. Alloy 600 vs Inconel?
Alloy 600 is a specific grade of Inconel, known for its resistance to oxidation and corrosion at moderate temperatures, while Inconel refers to a broader range of high-temperature resistant alloys, offering superior strength in extreme environments.
6. What is Inconel Alloy?
Alloy 600 is a nickel-chromium alloy with excellent resistance to oxidation and corrosion at moderate temperatures, while Inconel alloys (such as Inconel 625 or 718) provide superior high-temperature strength and oxidation resistance, making them ideal for extreme temperature and stress environments.