Huaxiao Metal – A Top Incoloy Alloy Manufacturer in China
Huaxiao Metal is a leading Incoloy alloy supplier in China, offering a broad range of high-performance alloys, including Incoloy 825, Incoloy 800, Incoloy 840, Incoloy Alloy 800H, Incoloy Alloy 800HT, Incoloy Alloy A286, Incoloy Alloy 020, Incoloy Alloy 20, Incoloy Alloy 330, Incoloy Alloy 925, and Incoloy Alloy 945X.
Our Incoloy alloys are known for their corrosion resistance, high-temperature stability, and excellent mechanical properties, making them ideal for industries like chemical processing, aerospace, and petrochemical. As trusted Incoloy 825 suppliers and Incoloy 925 specialists, we provide tailored solutions to meet diverse needs.
Whether you need Incoloy 800HT or Incoloy 840, Huaxiao Metal ensures top-quality products that deliver outstanding performance in the most demanding environments. Contact us today to learn more about our range of Incoloy alloys and find the right material for your application.
Incoloy Alloy Products
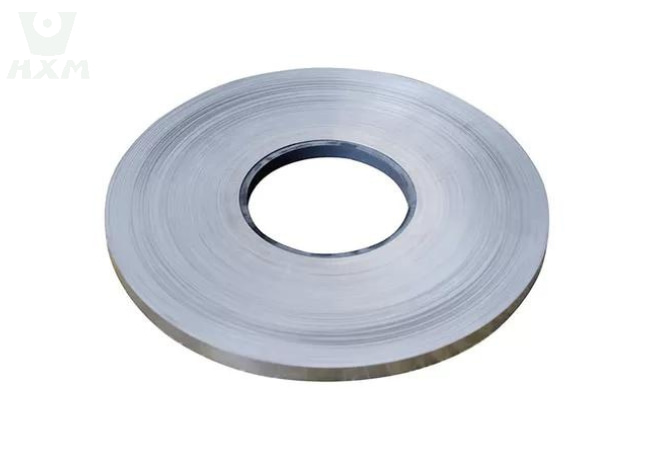
Incoloy Alloy 825
Previous slide Next slide Incoloy 825 Alloy Shapes: Plate & Sheet, Coil, Strip, Bar, Pipe & Tube, Wire & Mesh Grades: ASTM: B424 / UNS
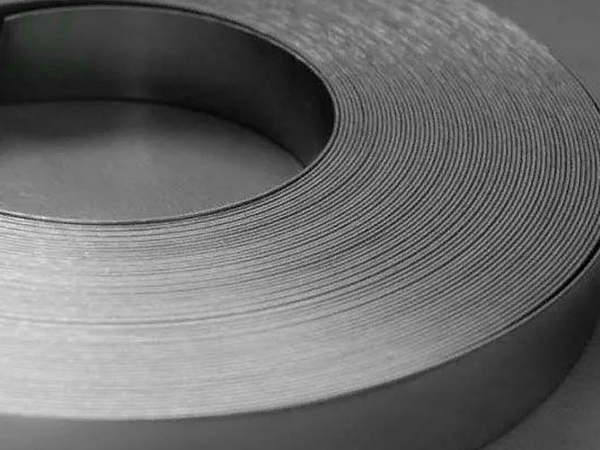
Incoloy Alloy 803
Previous slide Next slide Incoloy Alloy 803 Shapes: Plate & Sheet, Coil, Strip, Bar, Pipe & Tube, Wire & Mesh Grades: ASTM: A240 / S80300
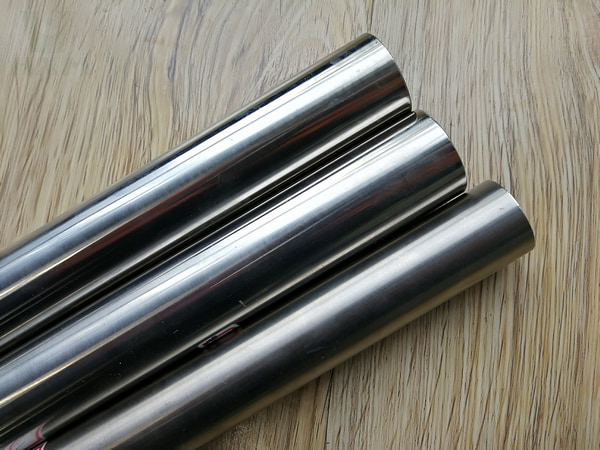
Incoloy Alloy 800
Previous slide Next slide Incoloy Alloy 800 Shapes: Plate & Sheet,Coil,Strip,Bar,Pipe & Tube,Wire & Mesh Grades: ASTM: A240 / S80000, S800H, S800HTJIS: G4304 / SUS800,
Incoloy Alloy Classification
Classification of Incoloy Alloys:
Incoloy alloys are available in various grades, each specifically designed to meet performance requirements across different industries. As a trusted Incoloy alloy supplier, we offer a wide range of alloys, including Incoloy alloy 800, Incoloy 800, Incoloy 840, Incoloy alloy 800H, Incoloy alloy 800HT, Incoloy alloy 825, Incoloy alloy A286, Incoloy alloy 020, Incoloy alloy 20, Incoloy alloy 330, Incoloy alloy 925, Incoloy alloy 945X, and more. Some of the most common types of Incoloy alloys we supply include:
Incoloy 800: Known for excellent resistance to oxidation and carburization, Incoloy 800 is widely used in heat exchangers, chemical processing, and furnace components. As leading Incoloy 800 suppliers, we provide high-quality solutions for these applications.
Incoloy alloy 800H: This high-strength version of Incoloy 800 offers improved creep resistance, making it ideal for more extreme high-temperature applications, such as in power plants and petrochemical processes. We are your reliable Incoloy alloy 800H supplier, offering this grade for demanding environments.
Incoloy alloy 800HT: Optimized for high-temperature strength at temperatures above 1100°F (593°C), Incoloy alloy 800HT is commonly used in steam generators and industrial furnaces. As a trusted Incoloy alloy 800HT supplier, we offer this alloy for the toughest high-temperature applications.
Incoloy alloy 825: Known for superior resistance to a wide range of corrosive environments, including sulfuric acid, phosphoric acid, and seawater, Incoloy alloy 825 is widely used in chemical processing and marine environments. As top Incoloy alloy 825 suppliers, we provide this alloy for industries requiring exceptional corrosion resistance.
Incoloy alloy 925: This alloy offers high strength and excellent resistance to both corrosion and oxidation, making it suitable for high-temperature, high-pressure applications such as gas turbines and petrochemical reactors. We supply Incoloy alloy 925 to meet the demanding requirements of these industries.
Incoloy alloy 330: Known for its excellent resistance to oxidation and carburization, Incoloy alloy 330 is often used in furnace components, heat exchangers, and gas turbines. As an experienced Incoloy alloy 330 supplier, we provide this alloy for high-performance applications.
Incoloy alloy 686: This high-performance alloy provides exceptional resistance to acids, especially in environments exposed to chlorides and sulfur compounds. It is commonly used in chemical plants and marine environments, and we supply this grade as part of our comprehensive Incoloy alloy offerings.
Incoloy alloy 693: Designed for high-temperature strength and good corrosion resistance, Incoloy alloy 693 is suitable for chemical processing, power plants, and other high-temperature environments. As an Incoloy alloy supplier, we provide this alloy for various industrial uses.
Incoloy alloy 832: Offering improved strength and resistance to high-temperature oxidation, Incoloy alloy 832 is commonly used in heat exchangers and other industrial applications. We provide this alloy as part of our extensive inventory of Incoloy alloys.
Incoloy alloy 944: Known for its exceptional strength and resistance to high-temperature corrosion, Incoloy alloy 944 is ideal for applications in severe environments such as aerospace and petrochemical industries. We supply Incoloy alloy 944 for these demanding sectors.
Incoloy alloy 945: With excellent high-temperature properties, Incoloy alloy 945 offers resistance to thermal fatigue and oxidation, making it a great choice for power generation and chemical processing industries. As a trusted Incoloy alloy 945 supplier, we provide this alloy for high-performance applications.
Incoloy alloy 945X: An advanced version of Incoloy alloy 945, Incoloy alloy 945X is designed for even higher strength and creep resistance at elevated temperatures. This alloy is ideal for the most demanding high-temperature applications, and as a leading Incoloy alloy 945X supplier, we offer it to meet your specific needs.
As a reputable Incoloy alloy supplier in China, we pride ourselves on providing high-quality products, including Incoloy 825 suppliers, Incoloy 925 manufacturers, and other grades available for sale to suit your unique requirements. Whether you’re looking for Incoloy alloy 800 suppliers, Incoloy 825 manufacturers, or competitive Incoloy 925 prices, we offer tailored solutions with stock availability for industries such as chemical processing, aerospace, petrochemical, and more. Contact us today to discuss your B2B needs and learn more about our comprehensive selection of Incoloy alloys at the best prices.
1. Alloy 800 (Incoloy 800)
- Composition: Nickel (30-35%), Chromium (19-23%), Iron (balance).
- Properties: Excellent oxidation and high-temperature resistance. Good strength and weldability.
- Applications: Used in boilers, heat exchangers, nuclear reactors, and chemical processing at high temperatures.
2. Alloy 803 (Incoloy 803)
- Composition: Nickel (25-30%), Chromium (20-23%), Iron (balance).
- Properties: Similar to Alloy 800, but offers improved creep resistance and slightly better corrosion resistance in reducing environments.
- Applications: Used in turbine components, combustion chambers, and high-temperature reactors.
3. Alloy 825 (Incoloy 825)
- Composition: Nickel (38-46%), Chromium (19-23%), Iron (balance), plus Molybdenum and Copper.
- Properties: Excellent corrosion resistance, especially in acidic environments. Good strength at high temperatures.
- Applications: Ideal for chemical processing, nuclear power, and acidic environments like sulfuric acid and marine applications.
Incoloy Alloy Advantages
Exceptional High-Temperature Resistance: Incoloy alloys, including Incoloy 800, Incoloy 825, Incoloy 925, and Incoloy 800H, offer outstanding strength and oxidation resistance at elevated temperatures. This makes them ideal for high-temperature applications in industries such as power generation, aerospace, and chemical processing. As a trusted Incoloy alloy supplier, we provide a range of Incoloy alloys, including Incoloy 800, Incoloy 840, and Incoloy 800H, perfect for these demanding environments.
Outstanding Corrosion Resistance: These Incoloy alloys, particularly Incoloy 825, Incoloy 925, and Incoloy alloy 020, exhibit superior resistance to a wide range of corrosive environments, including acids, alkalis, and chloride-induced corrosion. This ensures long-term performance in harsh chemical, marine, and industrial conditions. As leading Incoloy 825 suppliers, we offer these alloys for industries that require exceptional corrosion resistance in tough environments.
Superior Creep and Stress Rupture Resistance: Incoloy alloys, especially Incoloy 800H and Incoloy alloy 800HT, provide excellent resistance to creep and stress rupture under high-temperature conditions. These alloys are ideal for components exposed to continuous thermal and mechanical stress. As a top Incoloy alloy 800 supplier, we offer high-quality Incoloy 800H for applications that demand high resistance to thermal fatigue.
High Density and Strength: Incoloy alloys, especially those with higher nickel content such as Incoloy 925 and Incoloy 945X, have a higher density, which contributes to increased mechanical strength and durability. This makes them particularly suitable for demanding applications that require both toughness and resistance to wear. We, as Incoloy 925 manufacturers, offer these alloys with excellent mechanical properties for high-strength applications.
Versatility Across Applications: The unique combination of high strength, oxidation resistance, and corrosion resistance in Incoloy alloys makes them highly versatile. Whether it’s Incoloy 825 for chemical processing, Incoloy 800 for aerospace, or Incoloy alloy 20 for marine applications, these alloys are used in critical components such as heat exchangers, turbines, reactors, and pipes. As a reliable Incoloy alloy supplier in China, we provide an extensive range of Incoloy alloys to meet the specific needs of various industries.
Good Weldability and Fabricability: Incoloy alloys are known for their excellent weldability and ease of fabrication, allowing for the production of complex and custom components. This flexibility in manufacturing processes makes them suitable for various industries. As Incoloy alloy 800HT suppliers, we ensure that our alloys are easy to weld and fabricate, providing businesses with high-quality materials for custom projects.
Resistance to Oxidation and Scaling: Incoloy alloys excel in resisting oxidation and scaling, ensuring reliable performance in high-temperature environments. Alloys like Incoloy 840, Incoloy alloy A286, and Incoloy 925 are ideal for heat exchangers and boilers, where long-term durability is critical. As Incoloy alloy 840 suppliers, we provide these alloys with excellent oxidation resistance, ensuring your components remain reliable in the harshest conditions.
Stock Availability and Competitive Prices: At our company, we ensure stock availability of a wide range of Incoloy alloys such as Incoloy 825, Incoloy 925, and Incoloy alloy 330, providing competitive prices to meet the demands of our B2B customers. Whether you are looking for Incoloy 800 for sale or seeking high-quality Incoloy alloy 945X at the best price, we offer prompt delivery and customized solutions for B2B industries worldwide.
Applications of Incoloy Alloy
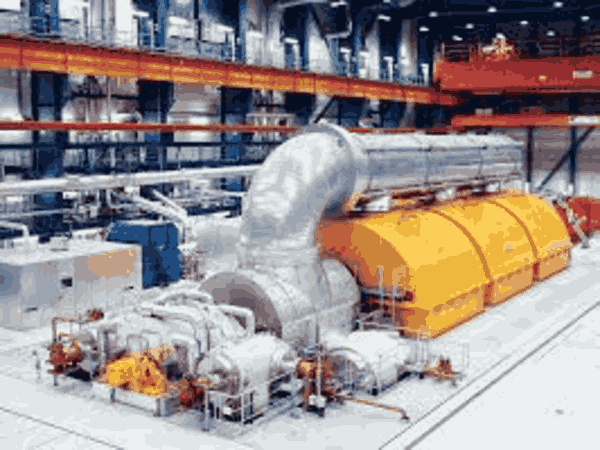
Power Generation
Incoloy are ideal for power plant components like boiler tubes and heat exchangers, offering strength, oxidation resistance, and thermal cycling durability.
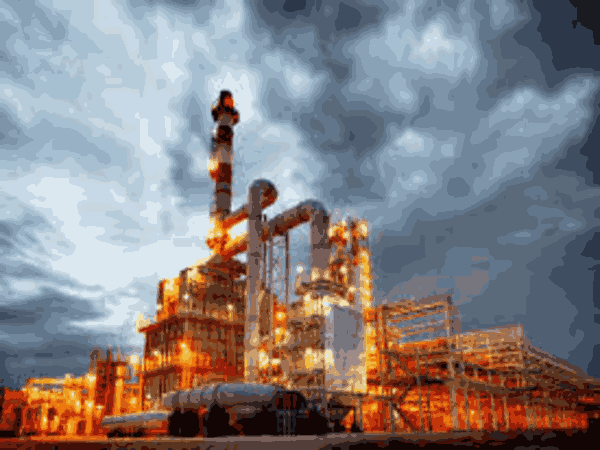
Oil and Gas Industry
Incoloy are used in the oil and gas industry for their resistance to extreme temperatures and harsh environments, including downhole tubing, gas turbines, and pumps.
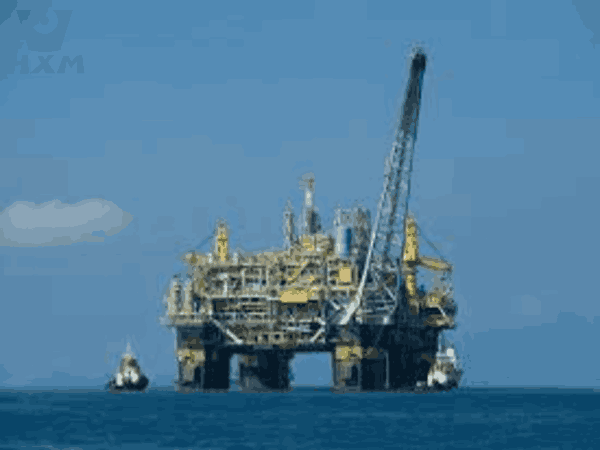
Marine Applications
Incoloy are used in marine applications like seawater heat exchangers and exhaust systems for their resistance to chloride corrosion and pitting.
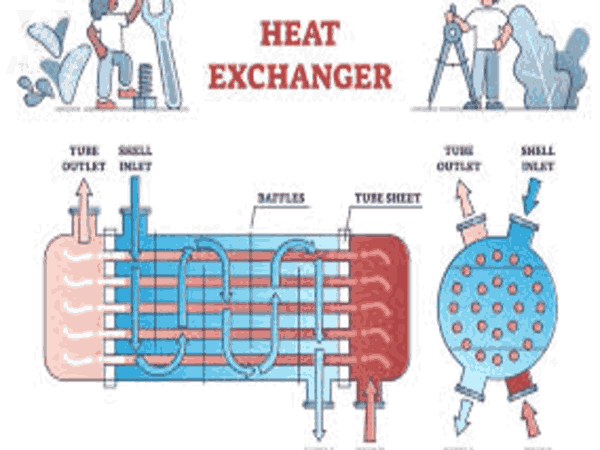
Heat Exchangers and Boilers
Incoloy are used in heat exchangers and boilers for their resistance to oxidation, scaling, and high-temperature corrosion.
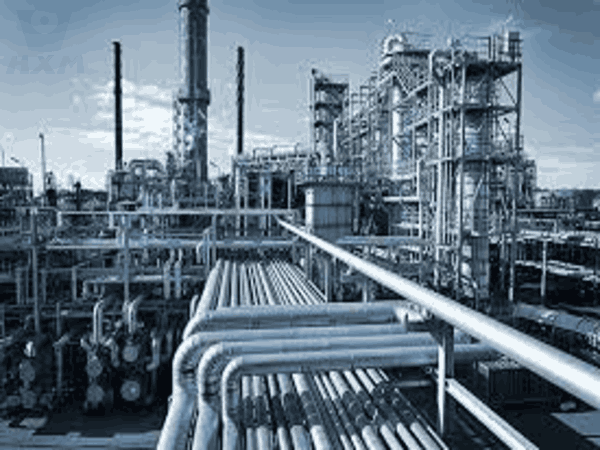
Chemical Processing
Incoloy are used in chemical processing for reactors, heat exchangers, and pipes exposed to high temperatures and corrosive chemicals.
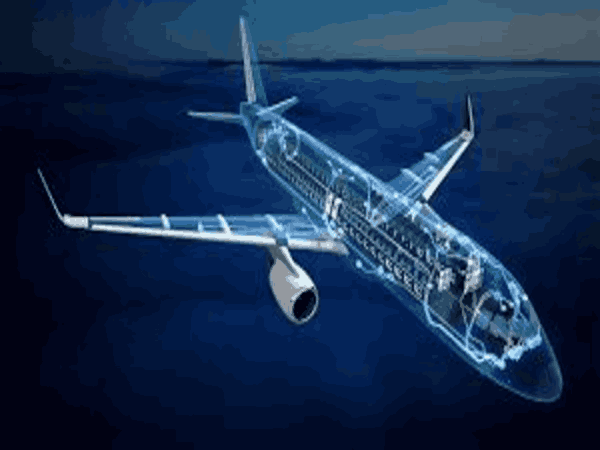
Aerospace
Incoloy are used in aerospace for turbine blades, exhaust systems, and other high-temperature parts due to their creep resistance and performance in extreme conditions.
If you are unsure about the applications of Incoloy alloys in various industries, you can contact us, Incoloy alloy supplier, to learn more.
FAQ
1. What is the chemical composition of Incoloy 825?
Incoloy 825 is a nickel-iron-chromium alloy with significant amounts of molybdenum, copper, and titanium, offering excellent resistance to corrosion.
2. Incoloy vs Inconel?
Incoloy and Inconel are both nickel-based alloys, but Incoloy has a higher iron content and is optimized for corrosion resistance, while Inconel is designed for high-temperature strength.
3. What is Incoloy material?
Incoloy is a group of corrosion-resistant, high-temperature alloys primarily composed of nickel, iron, and chromium.
4. Incoloy 825 vs Inconel 625?
Incoloy 825 is more corrosion-resistant, especially in acidic environments, while Inconel 625 excels in high-temperature strength and oxidation resistance.
5. Is Inconel and Incoloy the same?
No, they are different alloys: Inconel is focused on high-temperature resistance, while Incoloy is optimized for corrosion resistance.
6. What is the composition of an alloy?
An alloy’s composition refers to the specific mixture of metals and elements that make up the material, influencing its properties like strength, corrosion resistance, and heat tolerance.